AmargTank ClassicWeld® – dowiedz się, jak wygląda produkcja zbiorników z gotowych płyt tworzywa sztucznego
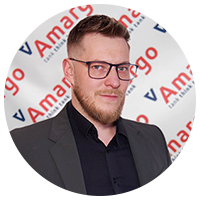
Grzegorz Zając, Ekspert z zakresu zbiorników i instalacji przemysłowych z tworzyw sztucznych
AmargTank ClassicWeld® – dowiedz się, jak wygląda produkcja zbiorników bezciśnieniowych z gotowych płyt tworzywa sztucznego
W niniejszym wpisie przybliżamy standardową metodę produkcji zbiorników bezciśnieniowych – AmargTank ClassicWeld® – z zastosowaniem gotowych arkuszy tworzyw sztucznych o stałych wymiarach handlowych: 2000 x 1000 mm, 3000 x 1500 mm i 4000 x 2000 mm oraz o określonych grubościach. Poza płytami do produkcji wykorzystywane są druty spawalnicze w formie zwojów. W zależności od wymaganych wymiarów zbiornika arkusze tworzywa są przycinane, a następnie zgrzewane doczołowo oraz spawane ekstruzyjnie lub gorącym powietrzem. Inną z metod jest technologia nawojowa (AmargTank SafeSeamLess®, MultiLayer® i MultiLayer DoubleWall®).
Charakterystyka technologii AmargTank ClassicWeld®
Technologia AmargTank ClassicWeld® znajduje zastosowanie w produkcji zbiorników magazynowych (także dozorowych UDT) lub procesowych dla szeregu substancji żrących, trujących i niebezpiecznych. O rodzaju tworzywa decyduje jego odporność chemiczna na dane medium (sprawdź wpis: Odporność chemiczna tworzyw PE i PP w kontekście projektowania i produkcji zbiorników chemoodpornych).
Produkując zbiornik w tej technologii należy mieć na uwadze, że o ile metoda znajduje sporą gamę zastosowań, ma ona pewne ograniczenia, które warunkują wykonanie zbiornika. Poniżej wymieniliśmy zalety technologii, a w dalszej części pewne bariery, które mogą decydować o zmianie sposobu wykonania (np. na metodę nawojową, omawianą w artykule Produkcja innowacyjnych zbiorników z tworzyw termoplastycznych metodą nawojową – co przemysł na niej zyska?).
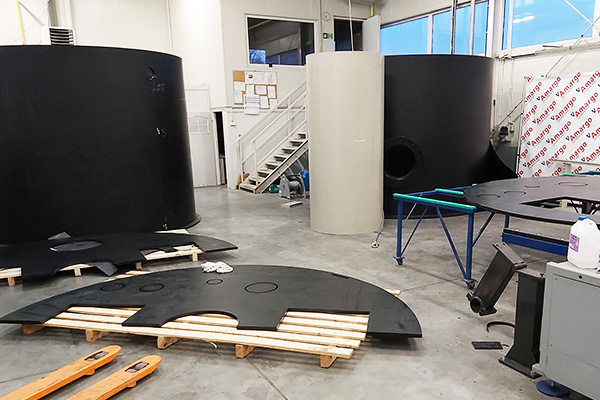
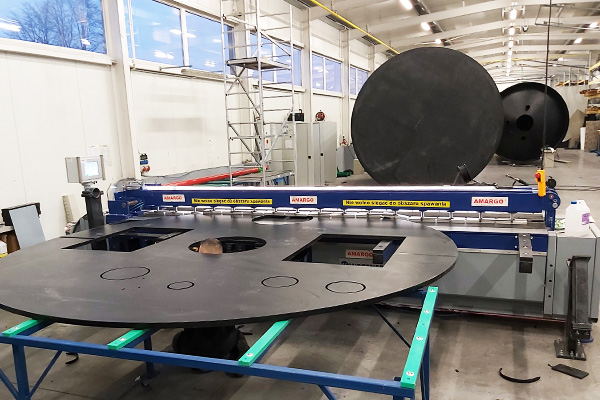
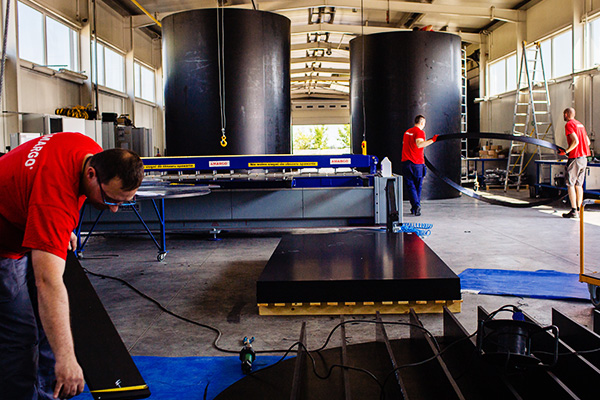
Zalety technologii AmargTank ClassicWeld®
- Do produkcji wykorzystywane są certyfikowane płyty tworzywa, które dzięki wysokiej odporności chemicznej pozwalają na bezpieczne magazynowanie chemikaliów.
- Stosowane tworzywa sztuczne posiadają atesty PZH, co pozwala na zastosowanie np. w branży spożywczej.
- Konstrukcja zbiornika jest szczelna i hermetyczna.
- Właściwości tworzywa sztucznego eliminują ryzyko korozji zbiornika oraz decydują o odporności na warunki atmosferyczne i promieniowanie UV.
- Technologia pozwala na wykonanie zbiorników cylindrycznych lub prostopadłościennych, do posadowienia zarówno wewnątrz, jak i na zewnątrz obiektu.
- Przy produkcji zbiorników z płyt tworzywa każdorazowo wykonujemy obliczenia statyki według norm DVS, co gwarantuje wieloletnią żywotność i wytrzymałość zbiornika.
- Zbiorniki są wykonywane z płyt, których krawędzie spajamy ze sobą za pomocą trwałego zgrzewania czołowego maszynowego według wytycznych DVS – dokumentacja powykonawcza zawiera protokoły zgrzein.
O tym warto pamiętać – ograniczenia przy produkcji zbiorników z gotowych arkuszy tworzywa sztucznego
- Wymiar zbiornika z gotowych płyt jest ograniczony przede wszystkim formatem arkuszy oraz obróbką mechaniczną i spawaniem/zgrzewaniem (maksymalnie 4 m długości i 30-50 mm grubości), co pozwala na wykonanie cylindra o wysokości do H = 4,0 m (w razie potrzeby można zastosować np. połączenia mufowe, fazowanie krawędzi, centrowanie czy spawy potrójne).
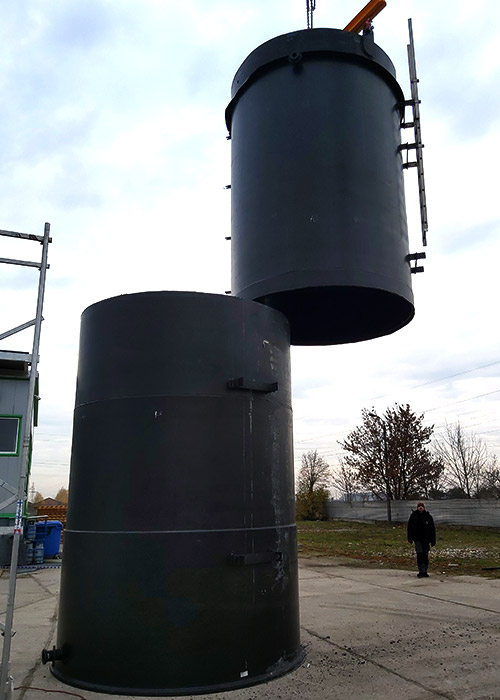
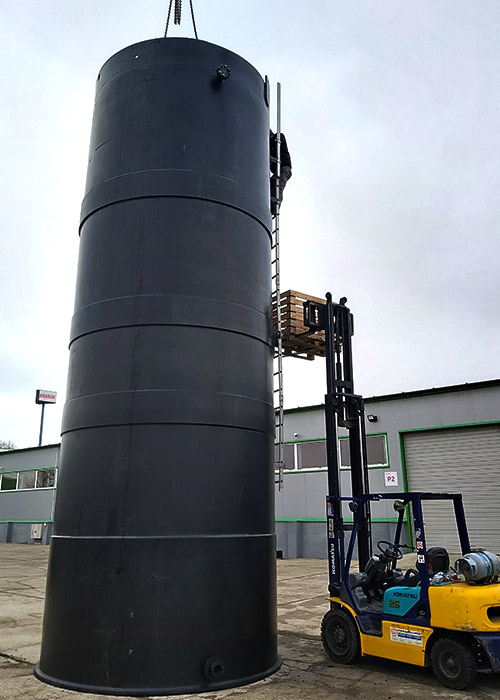
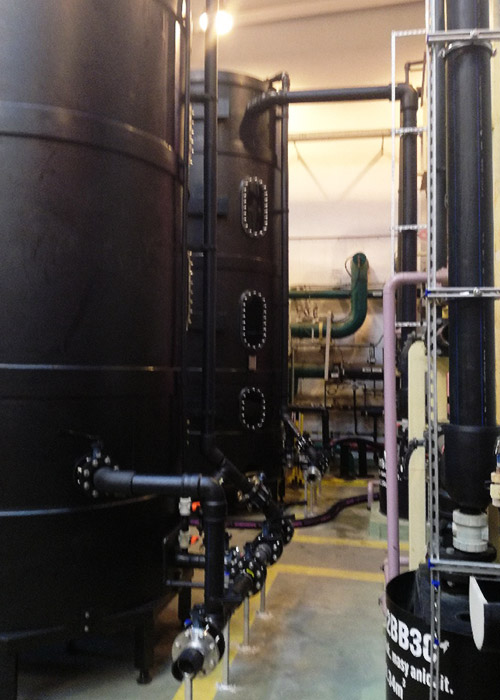
- Przy produkcji tą metodą należy uwzględnić współczynniki osłabienia miejsc spoin, zgrzein, spawów ściśle według wytycznych DVS, co wpływa na wzrost grubości ścianki, wagę zbiornika oraz ograniczenia w formowaniu cylindrów.
Możliwość wykonania cylindrów z płaskich płyt tworzywa wynika z zależności między grubością ścianek zbiornika a minimalną średnicą cylindra (mm), które określa norma DVS.
- Ze względu na brak możliwości zwijania płaskich arkuszy tworzywa powyżej określonej grubości płyty może okazać się, że założona średnica zbiornika nie może zostać zrealizowana z uwagi na ograniczenia normowe DVS w zakresie nieprzekraczania dopuszczalnych naprężeń wewnątrzmateriałowych.
- Produkcja zbiornika z gotowych płyt uniemożliwia wykonanie płynnego stopniowania grubości części cylindrycznej – każda carga musi być wykonana z arkuszy płyt stałej grubości.
W przypadku zbiorników o wysokościach np. 4 czy 6 m, w dolnej partii zbiornika ciśnienie/siły są większe. Tym samym w tym odcinku ścianka jest grubsza i zmniejsza się ku górze. W przypadku zbiorników produkowanych z płyt, zazwyczaj w kontekście ekonomicznym, wysokość odcinka o danej grubości jest zależna od wymiaru handlowego arkusza tworzywa. Dla przykładu, wykorzystując arkusz o wymiarach 3000 x 1500 mm jedną, większą grubość tworzywa stosujemy na wysokość zależną od szerokości płyty (w tym przypadku 1500 mm), dopiero wyżej cieńszą. W przeciwnym razie musimy się liczyć z nieco większymi kosztami ze względu na odpady materiału. W zależności od przeznaczenia alternatywą jest produkcja zbiornika metodą nawojową (rury nawijane helikalnie umożliwiają optymalne wykorzystanie tworzywa z odmienną grubością stopniowaną na przykład co 20–30 cm, w zależności od wysokości zbiornika).
- Technologia eliminuje możliwość zastosowania techniki detekcji nieszczelności międzyściankowej (co jest możliwe przy technologii AmargTank MultiLayer DoubleWall®) – w tym celu wykonujemy drugi płaszcz (zbiornik w zbiorniku) o pełnej wytrzymałości oraz wyposażamy zbiornik w czujnik wilgoci (na zasadzie przewodzenia elektrycznego) lub pływak.
Zbiorniki chemoodporne (szczególnie dozorowe), które pracują ze żrącymi i niebezpiecznymi substancjami wyposażamy we wskaźniki poziomu cieczy (sondy pomiaru bezkontaktowego: ultradźwiękowe lub radarowe z opcją retransmisji sygnałów oraz poziomowskazy pływakowe), a także czujniki przepełnienia zgodnie z wymaganiami UDT. Ponadto dobieramy optymalne technicznie i ekonomicznie rozwiązania zabezpieczające, którymi są:
- drugi płaszcz w konstrukcji zbiornika, pełniący funkcję wanny wychwytującej (tzw. zbiornik dwupłaszczowy),
- płaszcz z systemem monitorowania szczelności/wycieków,
- zbiornik w wannie zabezpieczająco-wychwytującej – dzięki temu zabezpieczeniu chronione są posadzki hal produkcyjnych oraz odpływy ściekowe.
- Brak możliwości stosowania różnych materiałów, warstw o różnych parametrach w zależności od miejsc stosowania, gdzie występuje ryzyko oparów wybuchowych – np. dla etanolu (strefy zagrożenia wybuchem) zasadne jest wykonanie z elektroprzewodzącego materiału pełnej grubości ścianki (w pełnym przekroju jednolity materiał z dodatkami spowoduje znaczny wzrost kosztów materiałowych). Taką możliwość daje technologia nawojowa.
Jak przebiega produkcja zbiornika bezciśnieniowego w technologii AmargTank ClassicWeld®?
Po weryfikacji wszystkich niezbędnych danych przystępujemy do produkcji zbiornika, którą realizujemy zgodnie z aktualnymi normami i rozporządzeniami, rygorystycznymi standardami normy DVS 2205 oraz precyzyjnymi zapisami normy zakładowej nr NZ-AM/14192/TERM/2020.
Poniżej opisaliśmy w skrócie poszczególne kroki procesu. W przypadku zbiorników podlegających pod dozór UDT (posiadamy uprawnienia Urzędu Dozoru Technicznego (UDT) do wytwarzania, modernizacji i naprawy zbiorników bezciśnieniowych i niskociśnieniowych do materiałów trujących lub żrących oraz ciekłych zapalnych), przed przystąpieniem do produkcji uzgadniamy dokumentację techniczno-projektową w Urzędzie Dozoru Technicznego. Inspektor UDT bierze także udział przy pierwszych próbach szczelności wyprodukowanego zbiornika oraz przy testach po posadowieniu zbiornika (próby szczelności są wykonywane niezależnie od tego, czy zbiornik jest dozorowy czy też nie), co zostaje potwierdzone protokołami wykonania czynności dozoru technicznego.
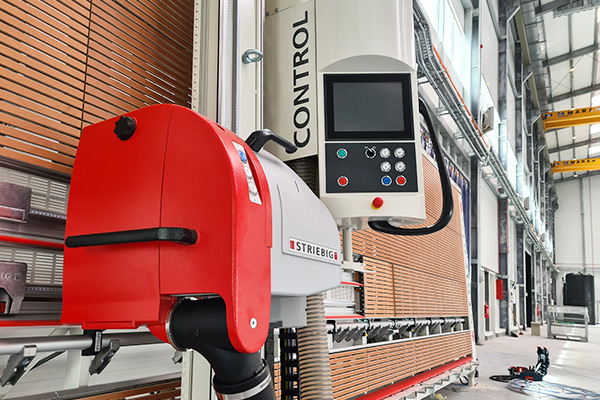
KROK 1
Sformatowanie płyty tworzywa – przycięcie krawędzi arkusza na wymiar, który będzie zgrzewany oraz zamocowanie płyty na zgrzewarce
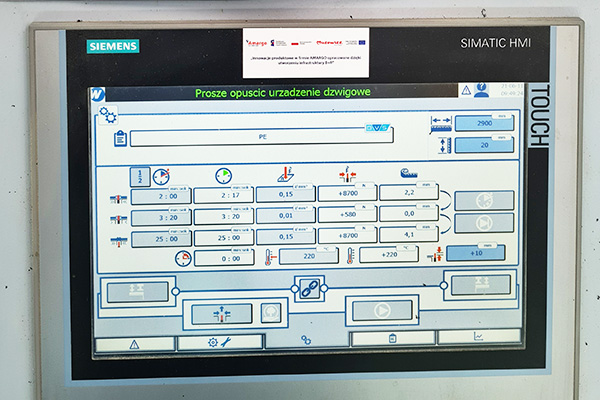
KROK 2
Zadanie parametrów płyty (materiał, długość zgrzewania, grubość arkusza) oraz ustawień zgrzewu zgodnie z aktualną normą DVS (wartości temperatury zadanej i rzeczywistej – zmierzonej)
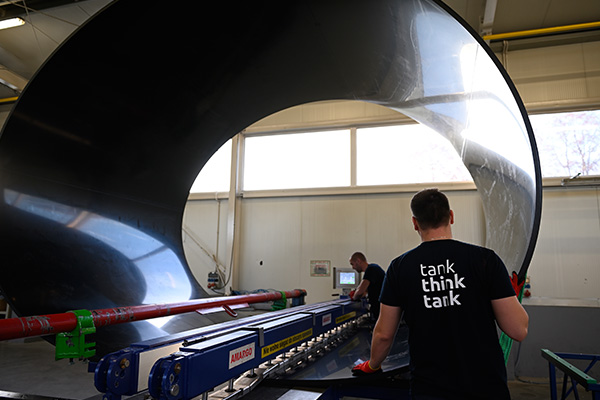
KROK 3
Etap I zgrzewania, czyli wyrównanie termiczne, które polega na wyrównaniu krawędzi płyt do miecza grzewczego (procesem cały czas steruje zgrzewarka)
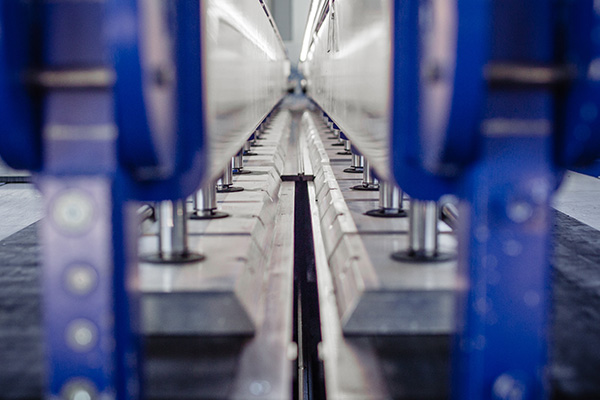
KROK 4
Etap II – grzanie, polegający na minimalnym docisku krawędzi płyty tworzywa do miecza grzewczego w określonym czasie
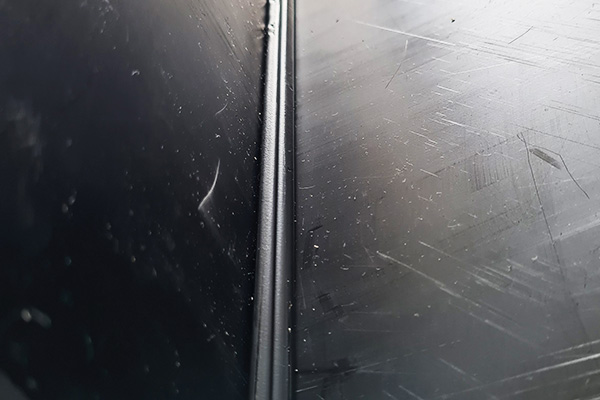
KROK 5
Etap III – docisk rozgrzanych krawędzi (jednym z punktów kontrolnych zgrzewu jest kształt wypływki tj. czy jej krawędzie są równe)
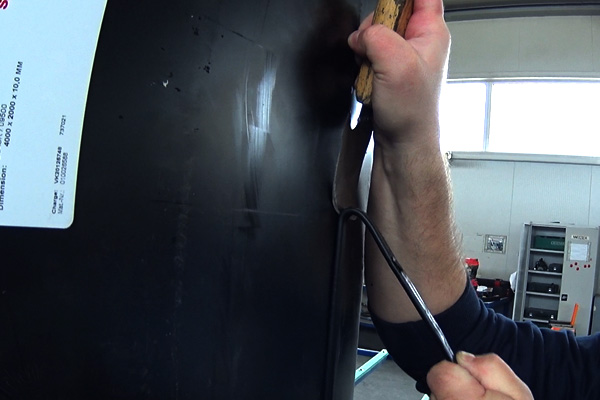
KROK 6
Proces zgrzewania się kończy – stoły podciśnieniowe automatycznie się podnoszą, uwalniając materiał – można wyjąć cylinder ze zgrzewarki i ściąć wypływkę
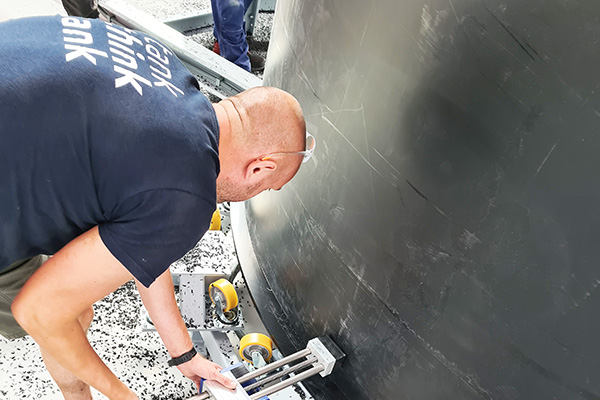
KROK 7
Ściany cylindra są scalane z dnem i dachem zbiornika za pomocą spawania ekstruzyjnego
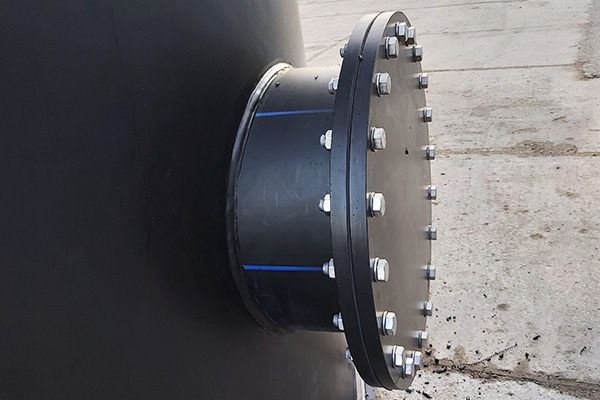
KROK 8
W zależności od konfiguracji zbiornika kolejnym etapem jest montaż króćców i włazów
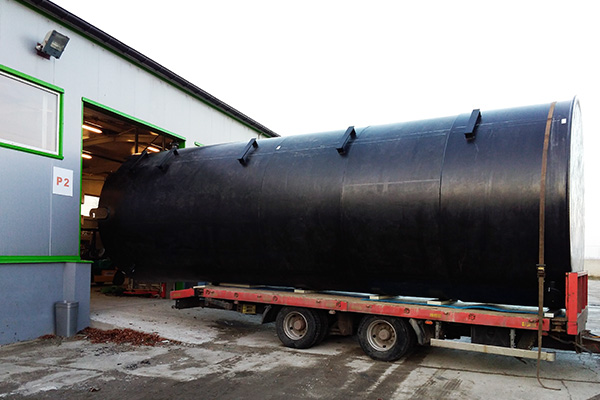
KROK 9
Gotowy zbiornik dostarczamy i montujemy na obiekcie Inwestora oraz wyposażamy w niezbędną armaturę
Zastosowanie zbiorników produkowanych z gotowych płyt tworzywa sztucznego
Zbiorniki chemoodporne produkowane z gotowych arkuszy tworzywa sztucznego znajdują zastosowanie przy magazynowaniu substancji żrących, trujących i niebezpiecznych (w tym także zbiorniki podlegające pod dozór UDT) oraz są wykorzystywane w procesach technologicznych realizowanych w przedsiębiorstwach przemysłowych (np. zbiorniki procesowe do przetwarzania produktów).
W celu zoptymalizowania kosztów opracowaliśmy typoszereg bezciśnieniowych zbiorników magazynowych wykonanych z PE100 i o pojemnościach od 1,6 m3 do 21 m3. Są one przeznaczone do przechowywania ługu sodowego NaOH 50%, kwasu solnego HCl oraz koagulantów PIX/PAX.
Materiały wykorzystywane do produkcji zbiorników chemoodpornych
Zbiorniki o materiałowo jednorodnej ściance (zgrzewane z ekstrudowanych płyt lub z rur beznaprężeniową technologią nawojową – ekstrudowanej wstęgi tworzywa: ścianka lita/strukturalna) | a) PE High Density UV (PE-HD, HDPE) – polietylen o dużej gęstości, stosowany np. do produkcji zbiorników magazynowania ługu sodowego b) PE100 RC – polietylen charakteryzujący się dużą wytrzymałością na obciążenia udarowe oraz nadzwyczajną odpornością na powolną propagację pęknięć (według ISO 13479 8760 h vs. >1000 h dla HDPE) c) homopolimer polipropylenu PP-H (dobra odporność chemiczna na działanie większości związków organicznych) d) kopolimer polipropylenu PP-C (podwyższona udarność także w niższych temperaturach, zakres użycia od −20 do +80oC) e) polichlorek winylu (stosowany również jako wkład do zbiornika z innego tworzywa) typ PVC-U lub PVC-C |
Zbiorniki o układzie warstwowym | a) płaszcz zewnętrzny z PEHD, wkład z PVC b) płaszcz zewnętrzny z PEHD, wkład z PVDF/E-CTFE – ze względu na koszty są one stosowane w małych grubościach jako linery, np. od 2–3 do maks. 4 mm |
Zbiorniki kompozytowe | żywice chemoodporne wzmacniane włóknem szklanym (GRP, FRP, TWS): a) układ żywic pokryty warstwą wykańczającą b) konstrukcje wielowarstwowe, np. liner wewnętrzny z tworzywa PE, PP, PVC, PVDF, E-CTFE, PFA (zapewniający niezwykle wysoką odporność chemiczną i temperaturową) + jako konstrukcja kompozyt o wysokiej odporności antykorozyjnej i chemicznej |
Przykłady zbiorników wyprodukowanych w technologii AmargTank ClassicWeld®
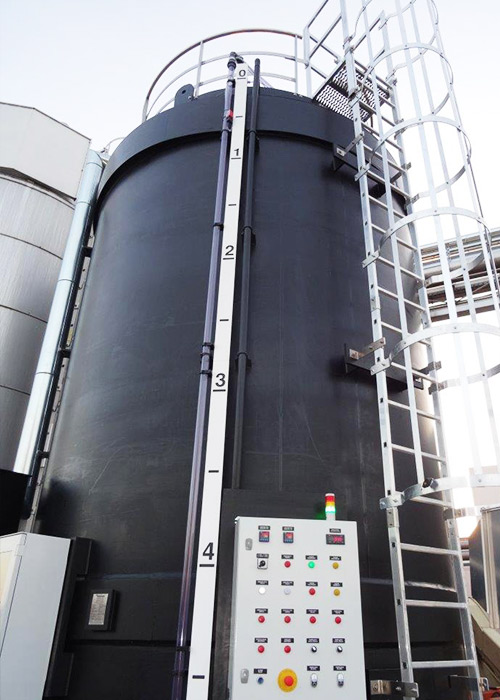
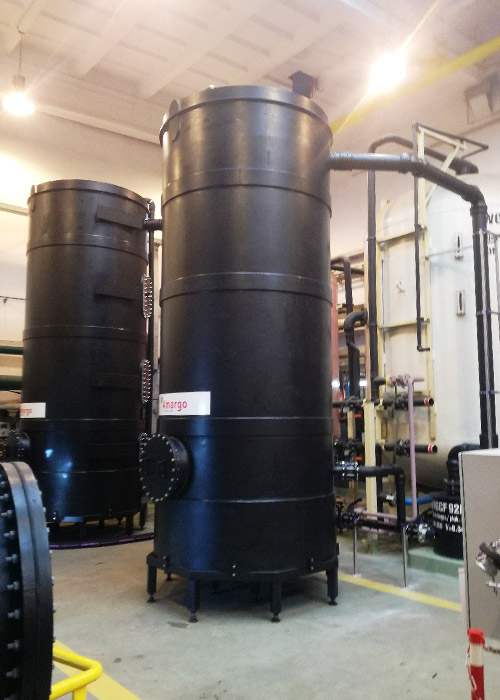
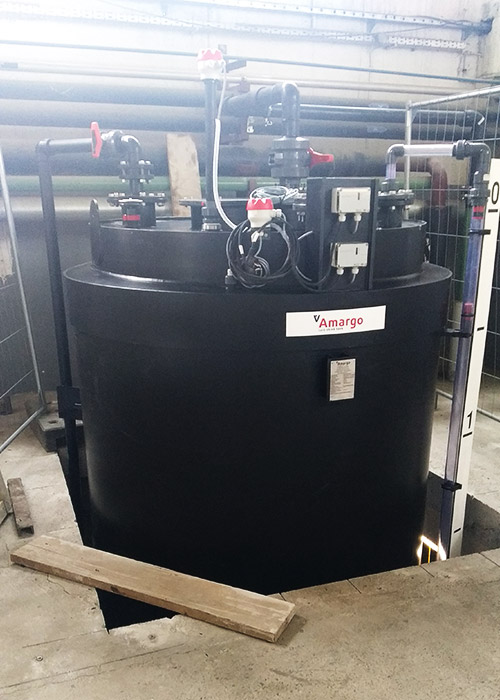
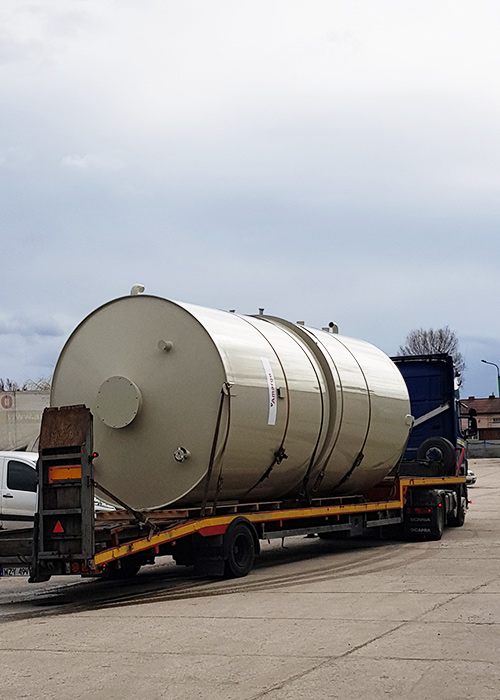
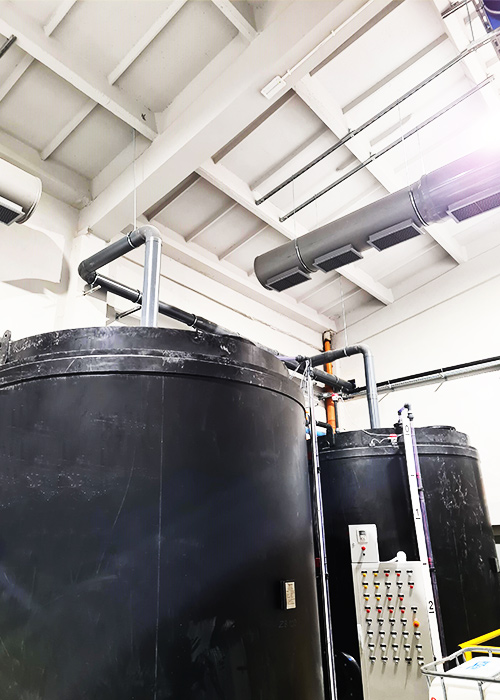
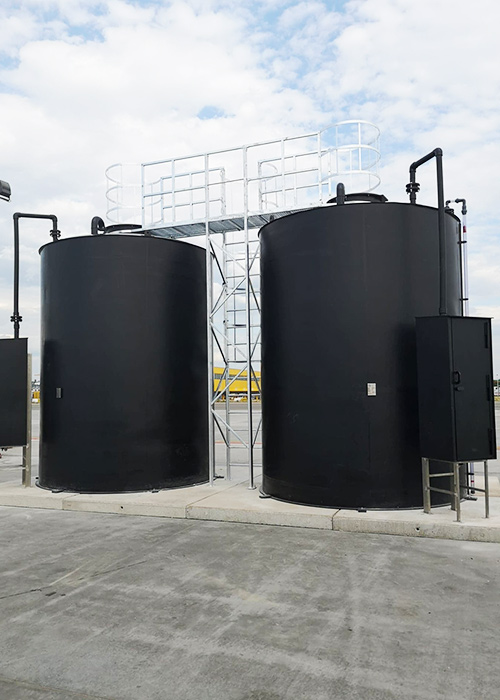
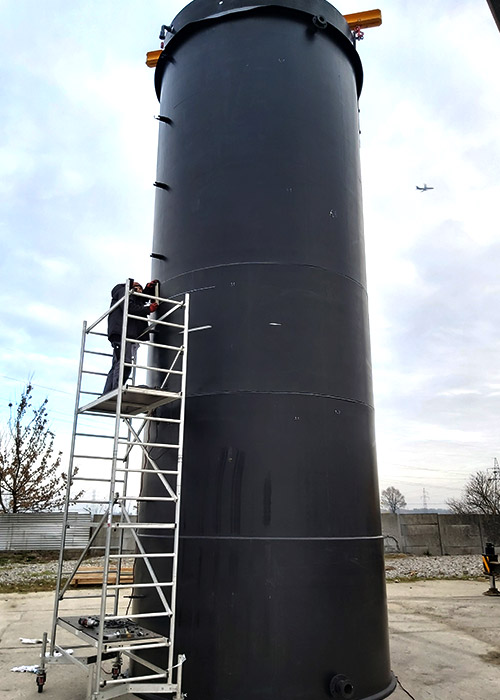
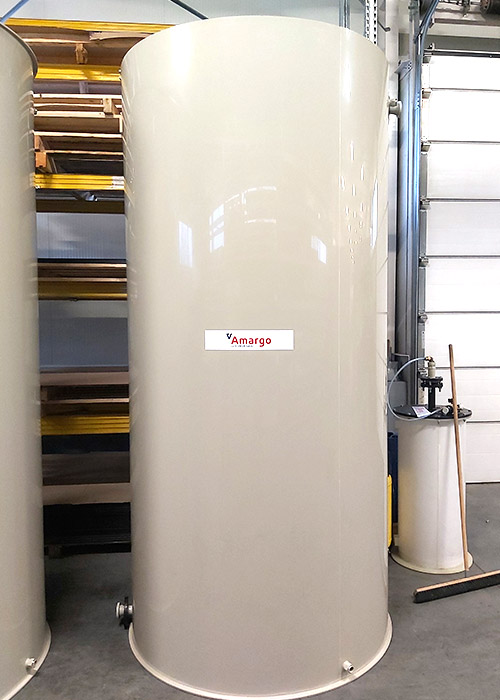
wodę oczyszczoną i wodę demineralizowaną
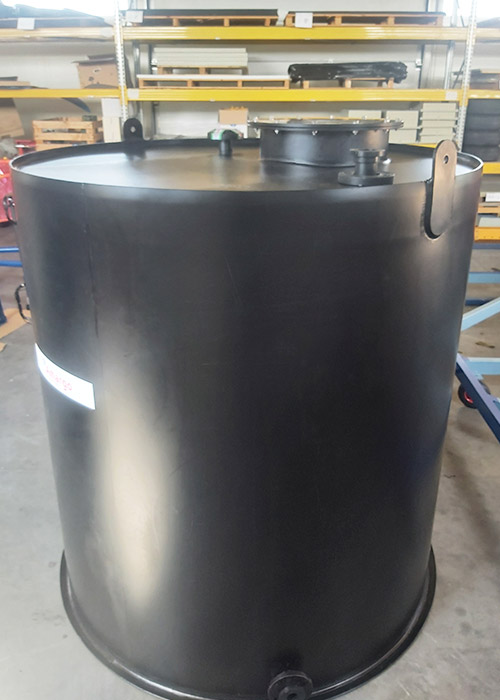
Porozmawiajmy o rozwiązaniu Twojego wyzwania
Rozmowa to klucz do sukcesu. Skorzystaj z naszej wiedzy i doświadczenia.