Zasady projektowania zbiorników magazynowych dozorowych z tworzyw sztucznych
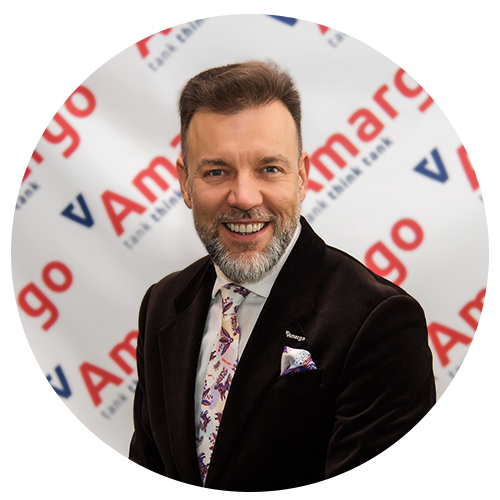
Autor: Szczepan Gorbacz, Prezes Zarządu Amargo
Ekspert z zakresu zbiorników i instalacji z tworzyw sztucznych
Konsultacja merytoryczna: Leszek Lewandowski, Ekspert niezależny ds. Tworzyw Sztucznych
Pracownik Urzędu Dozoru Technicznego w latach 1984–2023 UDT Oddział w Bydgoszczy
Magazynowanie substancji żrących, trujących i ciekłych zapalnych wykorzystywanych w procesach przemysłowych często odbywa się w wielkogabarytowych układach zbiorników. Warunki przechowywania medium w takim zbiorniku muszą spełniać najwyższe standardy tak, by parametry fizykochemiczne kwasów czy zasad (takie jak np. temperatura, czystość, barwa) nie ulegały zmianom w okresie magazynowania. Ogromne znaczenie mają też warunki eksploatacji zbiornika i okres jego żywotności.
Projektowanie konstrukcji zbiorników na substancje żrące, trujące i ciekłe zapalne wymaga zwrócenia szczególnej uwagi na właściwości wytrzymałościowe oraz eksploatacyjne dobieranego materiału konstrukcyjnego. Mają one kluczowy wpływ na zapewnienie wysokiego poziomu bezpieczeństwa, gwarancję określonej żywotności zbiornika, koszty eksploatacyjne oraz sprostanie nowym trendom, m.in. w zakresie zrównoważonego rozwoju.
Dobór materiału konstrukcyjnego zbiorników
Na etapie koncepcji i projektowania ważne jest określenie przez inwestora najważniejszych parametrów pracy projektowanego zbiornika.
Uwzględniane są następujące informacje:
- rodzaj czynnika (medium) roboczego,
- parametry czynnika roboczego (temperatura, stężenie, gęstość, ciśnienie),
- miejsce posadowienia zbiornika (wewnątrz lub na zewnątrz budynku),
- temperatura i warunki otoczenia, w jakich będzie pracował zbiornik (np. czy będzie występowało promieniowanie cieplne od maszyn, naprężenia montażowe lub z instalacji, oddziaływanie wiatru i śniegu).
Parametry czynnika roboczego, przede wszystkim temperatura oraz stężenie, wpływają na dobór odpowiedniego tworzywa oraz grubość materiału ścian zbiornika, która zapewni odpowiednią statykę konstrukcji.
W inżynierii przemysłowej szczególną rolę odgrywają właściwości chemoodporne materiału. Oddziaływanie czynników chemicznych na polimery jest znacznie szybsze niż w przypadku wpływu czynników atmosferycznych.
Na odporność chemiczną kluczowy wpływ mają niżej wskazane warunki i parametry.
- Temperatura – wpływa na wytrzymałość mechaniczną
- wraz z jej wzrostem zwiększa się szybkość reakcji chemicznych, szybkość pęcznienia i ługowania,
- przy ujemnych temperaturach należy dobrać i przystosować tworzywa do zastosowania zewnętrznego;
- Promieniowanie ultrafioletowe;
- Zmienność warunków użytkowania – cykliczne zmiany są bardziej szkodliwe niż praca ciągła;
- Ruch cieczy – jej mieszanie zwiększa jej agresywność; Stężenie czynnika agresywnego.
Z uwagi na specyfikę warunków pracy wśród podstawowych materiałów konstrukcyjnych zbiorników należy wyróżnić tworzywa polimerowe z grupy termoplastów, m.in. PE100, PE100 RC, PP-H, PP-C, PCV, PVC-U, PVC-C, PVDF, E-CTFE, PFA, a także duroplasty – żywice GRP/TWS/FRP – konstrukcje kompozytowe poliestrowe i winyloestrowe oraz hybrydowe konstrukcje zespolone: liner chemoodporny i ścianka konstrukcyjna z kompozytu szklanego.
W wielu procesach technologicznych wykorzystywane są substancje o znacznym stężeniu i gęstości oraz wysokiej temperaturze pracy dochodzącej do 100°C dla tworzyw termoplastycznych, a w przypadku zbiorników z laminatów temperatury maksymalne osiągają wartość 180°C. Przy dodatkowych ograniczeniach przestrzeni, podczas doboru zbiornika z tworzyw termoplastycznych, może okazać się, że zachowanie geometrii nie pozwoli zapewnić jego odpowiedniej pojemności.
Z powodu sztywności oraz wysokiej wartości modułu sprężystości tworzyw termoplastycznych dąży się do ograniczenia powstawania szkodliwych naprężeń wewnątrzmateriałowych w wyniku zwijania arkuszy. Poza wpływem parametrów medium decydujące mogą być więc obliczenia wykonywane zgodnie z wytycznymi DVS [4] (Niemieckie Towarzystwo Spawalnicze – niem. Deutscher Verband für Schweißen und verwandte Verfahren eV.), jeśli chodzi o wybór technologii produkcji.
Konieczność zastosowania znacząco większych grubości ścianek dla zachowania odpowiedniej statyki konstrukcji może przesądzić o wykluczeniu standardowej technologii produkcji z wykorzystaniem gotowych arkuszy tworzywa (AmargTank ClassicWeld®). W takich przypadkach doskonałą alternatywą staje się technologia nawojowa (AmargTank SafeSeamLess®). Znajduje ona zastosowanie w szczególności dla zbiorników na kwas siarkowy i inne substancje o właściwościach silnie utleniających, które często wywołują efekt wyraźnych pęknięć naprężeniowych w zgrzewach lub spoinach arkuszy płyt zbiornika.
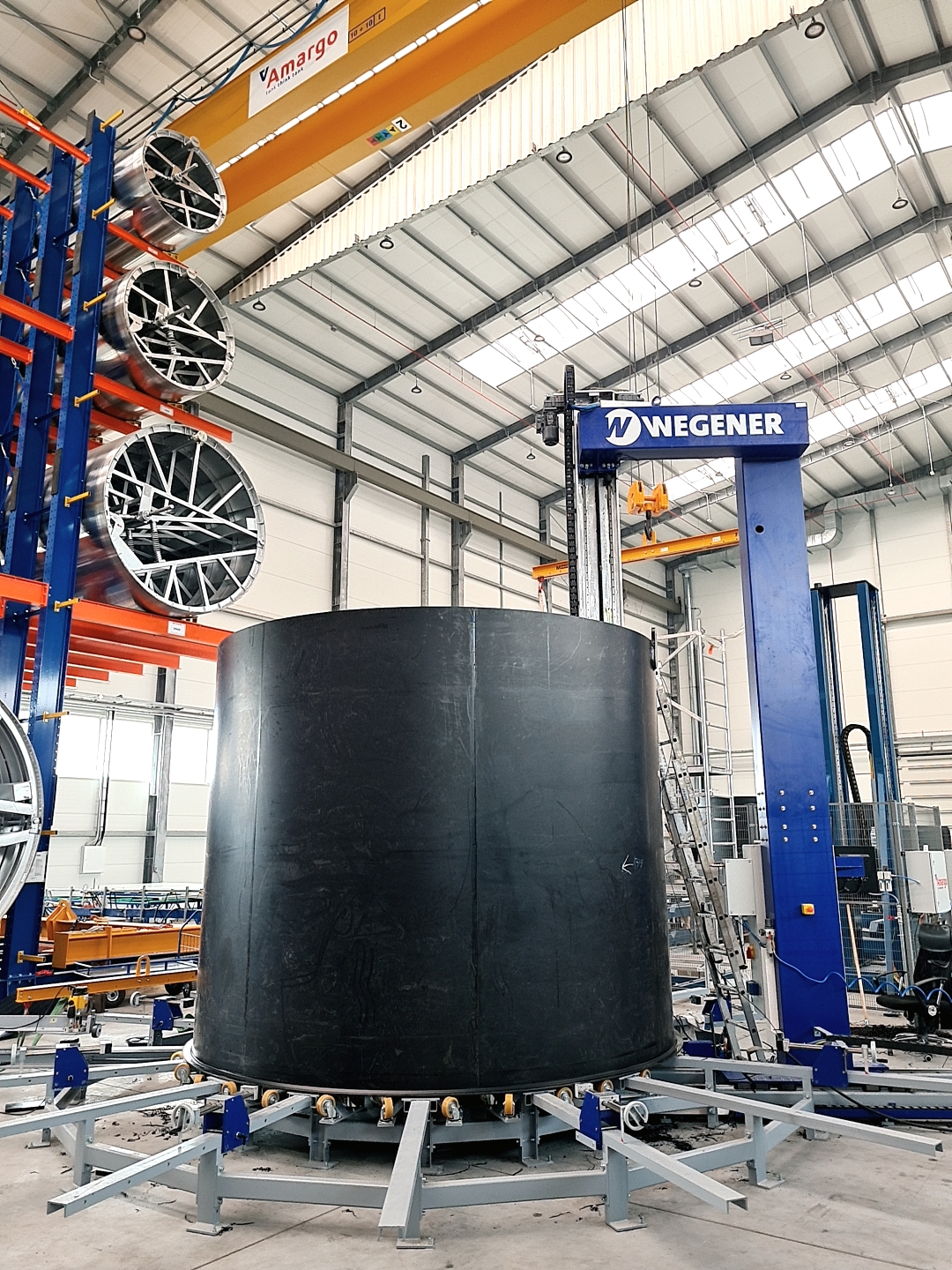
*AmargTank ClassicWeld® – nazwa własna standardowej technologii produkcji zbiorników bezciśnieniowych z zastosowaniem gotowych arkuszy tworzyw sztucznych o stałych wymiarach handlowych. Poza płytami do produkcji wykorzystywane są druty spawalnicze w formie zwojów. W zależności od wymaganych wymiarów zbiornika arkusze tworzywa są przycinane, a następnie zgrzewane doczołowo oraz spawane ekstruzyjnie lub gorącym powietrzem.
**AmargTank SafeSeamLess® – nazwa własna technologii nawojowej, która opiera się na systemie równolegle ekstrudowanych ścianek i profili nakładanych w jednoczesnym procesie wraz z podgrzewaniem stalowego obrotowego rdzenia prowadzącego. W kolejnym etapie następuje dalsza obróbka znana z sektora termoplastów. W efekcie powstaje bezspoinowa, uformowana na dany kształt i wymiar rura, czyli część cylindryczna zbiornika – pobocznica.
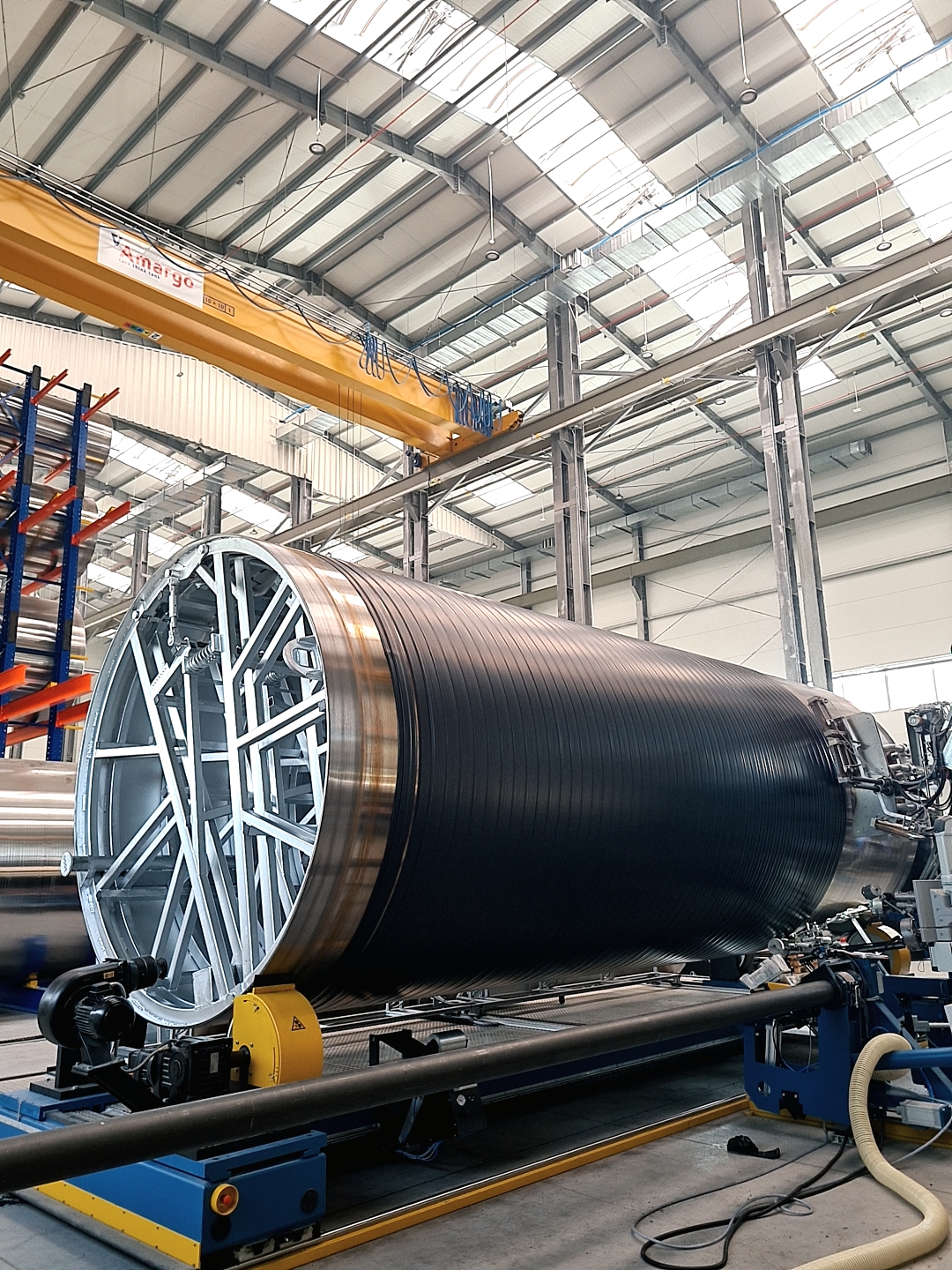
Temperatura czynnika roboczego, ze względu na właściwości medium, stanowi także istotny parametr pracy zbiornika, ponieważ ma wpływ na czas użytkowania jako zbiornika magazynowego. Żywotność zbiorników zależy bowiem od temperatury, która ogranicza czas ich pracy. Tę zależność w czasie dla poszczególnych grup tworzyw przedstawiono w tabeli 1.
Efekt „starzenia termicznego” jest zależny od temperatury, czasu oddziaływania, medium oraz zawartości tlenu.
Rodzaj tworzywa | Maksymalny czas użytkowania [lata] w zależności od temperatury [°C] | |||||||||
20 | 30 | 40 | 50 | 60 | 70 | 80 | 90 | 100 | 120 | |
PVC-U | 50 | 50 | 50 | 30 | 30 | – | – | – | – | – |
PVC-C | 50 | 50 | 50 | 30 | 30 | 20 | 20 | 20 | – | – |
PE-HD | 50 | 50 | 50 | 15 | 5 | 1 | – | – | – | – |
PP | 50 | 50 | 50 | 50 | 50 | 25 | 20 | 20 | 1 | 1 |
PVDF | 50 | 50 | 50 | 50 | 50 | 50 | 35 | 10 | 10 | 5 |
W kontekście projektowanej maksymalnej temperatury pracy, według zapisów DVS 2205 – 2 Działu 4.1 Strength analysis, w podpunkcie 4.1.2 [4] pod uwagę brane są występujące naprężenia w konstrukcji zbiornika, tzw. existing stress in the tank (N/mm2), oraz wartość maksymalna dopuszczalna przy określonym czasie, odczytana dla danego użytego materiału (N/mm2), których stosunek powinien być mniejszy bądź równy 1.
Dla zbiornika zaprojektowanego np. na 30°C temperatury pracy, dla pewnych warunków i materiałów, rzędu 70–80°C może być niszcząca, gdyż zostaną przekroczone dopuszczalne maksymalne wartości wytrzymałościowe danego materiału.
Bardzo ważna i zalecana jest zatem odpowiednia kultura pracy służb eksploatujących oraz świadomość różnic między poszczególnymi materiałami. Głównie chodzi o zmianę przyzwyczajeń w kontekście zbiorników stalowych z wężownicami zasilanymi parą wodną – zbiornik stalowy jest zdecydowanie bardziej odporny na przegrzewanie.
Projektując pracę zbiornika na substancje żrące, trujące i ciekłe zapalne, należy uwzględnić miejsce posadowienia zbiornika, tj. wewnątrz lub na zewnątrz obiektu. Lokalizacja posadowienia warunkuje:
- rodzaj zastosowanego tworzywa pod kątem odporności na promieniowanie UV oraz na niskie temperatury,
- kształt dachu (według DVS 2205 w przypadku zbiornika zewnętrznego dach powinien mieć kształt stożka z optymalnie dobranym kątem 15°) oraz zabudowę ewentualnego daszku po zewnętrznej stronie płaszcza głównego zbiornika – dotyczy sytuacji zabudowy dla zbiornika z wanną wychwytującą w celu zapobiegnięcia napływowi wody opadowej do przestrzeni międzypłaszczowej, co powodowałoby fałszywe alarmy z sondy wycieku,
- ocieplenie zbiornika – zależnie od rodzaju tworzywa i wrażliwości na warunki zewnętrzne oraz wymagań dotyczących np. temperatury przechowywania (takim medium jest np. ług sodowy).
Na rodzaj tworzywa zastosowanego do budowy zbiornika wpływ ma zatem także minimalna i maksymalna temperatura otoczenia. Tworzywem najbardziej odpornym na zewnętrzne całoroczne wahania temperatury (zwłaszcza poniżej -20°C) jest polietylen (PE). Tworzywa nieodporne na ujemne temperatury to głównie poli(chlorek winylu) (PVC) oraz polipropylen (PP). W przypadku zastosowania tych materiałów nie zaleca się transportu, montażu oraz eksploatacji zbiorników w niskich temperaturach, w których tworzywa te stają się zdecydowanie bardziej kruche i tym samym łatwiej podatne na uszkodzenia lub pęknięcia.
Odrębną kwestią jest odporność na promieniowanie UV. Polietylen odznacza się praktycznie pełną odpornością. Pozostałe tworzywa sztuczne stają się odporne na promieniowanie UV po dodaniu specjalnych stabilizatorów podczas wytwarzania.
Pojemność robocza zbiorników
Pojemność robocza jest istotna dla użytkownika pod kątem zapewnienia ciągłości produkcyjnej. Podczas projektowania zbiorników bezciśnieniowych i niskociśnieniowych należy bezwzględnie pamiętać o maksymalnej pojemności roboczej wynikającej z zapisów § 9 rozporządzenia Ministra Gospodarki [1] oraz § 9 rozporządzenia Ministra Gospodarki [2]:
„W przypadku, gdy w zbiorniku czynnikiem roboczym jest ciecz, należy pozostawić wolną przestrzeń w celu zabezpieczenia przed przelaniem się cieczy lub trwałym odkształceniem zbiornika zamkniętego w wyniku powiększenia się objętości cieczy pod wpływem wzrostu temperatury. Napełnienie zbiornika cieczą w najwyższej temperaturze roboczej nie powinno przekraczać 97% pojemności zbiornika”.
Zapisy rozporządzenia są wiążące w pierwszej kolejności, nie precyzuje ono jednak zasad projektowania realizowanego według standardów DVS 2205 [4] lub normy PN-EN 12573-2:2004 [3]. Według zapisów DVS [4]:
„Dopuszczalny stopień napełnienia zbiorników nie może przekraczać 95% pojemności”.
Finalnie taka wartość jest przyjmowana w projektowaniu i jest to jednocześnie wartość spełniająca kryterium z rozporządzenia.
Kształt projektowanego zbiornika
Najbardziej popularnym kształtem zbiorników magazynowych z tworzyw termoplastycznych jest cylindryczny o osi pionowej. Zapewnia optymalny rozkład naprężeń w odniesieniu do potrzebnej grubości materiału, liczby oraz typu wzmocnień. Zbiorniki te są stosunkowo nisko kosztowe w produkcji, a ich kształt zapewnia wytrzymałość związaną z ciężarem czynnika roboczego.
Podczas obliczeń statyki kalkulowane są również wszelkie miejsca osłabienia wynikające z rozlokowania króćców i włazów, zwłaszcza tych o znacznych średnicach i zlokalizowanych w dolnej części zbiornika. Należy to analizować na etapie wytwarzania oraz gdy inwestor rozważa modernizację zbiornika polegającą na dodaniu np. włazu bocznego w dolnej części zbiornika.
Projektowana żywotność zbiorników i element wskaźnikowy
Na etapie projektowania konstrukcji określana jest jej żywotność (tj. czas pracy) wyrażona w latach. Może to być okres na przykład 5, 10, 15 czy 20 lat. W zależności od tego czasu program do obliczeń statyki zbiornika wskazuje na odpowiednią grubość dna i pobocznicy wynikające z zadanego czasu żywotności.
W przypadku zbiorników chemoodpornych magazynowych, które będą pracowały z medium silnie żrącym, trującym lub ciekłym zapalnym oraz dodatkowo o charakterze utleniającym, na projektowaną żywotność zbiornika wpływ ma szereg innych parametrów. Projektując czas pracy zbiornika, należy mieć na uwadze warunki pracy, takie jak temperatura robocza i maksymalna, temperatura otoczenia czy ekspozycja zbiornika, tj. czy jest to zbiornik zewnętrzny poddawany zarówno promieniowaniu UV, jak i wpływom zmiennych temperatur ujemnych lub dodatnich.
Tematyka badań technicznych zbiorników podlegających dozorowi technicznemu i oceny możliwości wydłużenia okresu żywotności zbiorników jest zagadnieniem wymagającym odrębnego omówienia. Należy jednak w tym miejscu wspomnieć o stosowanych w konstrukcji zbiorników Amargo® wskaźnikach jakości spoin pozwalających na ocenę degradacji tworzywa podczas rewizji wewnętrznej.
Elementy wskaźnikowe montowane w każdym nowo produkowanym zbiorniku są wykonane z identycznego tworzywa i partii materiału jak cały zbiornik, wraz z próbkami spoin, i montowane na stałe w najniższej części zbiornika. Dzięki temu są poddane ciągłej pracy z pełnym obciążeniem chemicznym. Na tej podstawie można ocenić stan techniczny konstrukcji i świadomie podjąć decyzję o ewentualnym przedłużeniu okresu eksploatacji zbiornika.
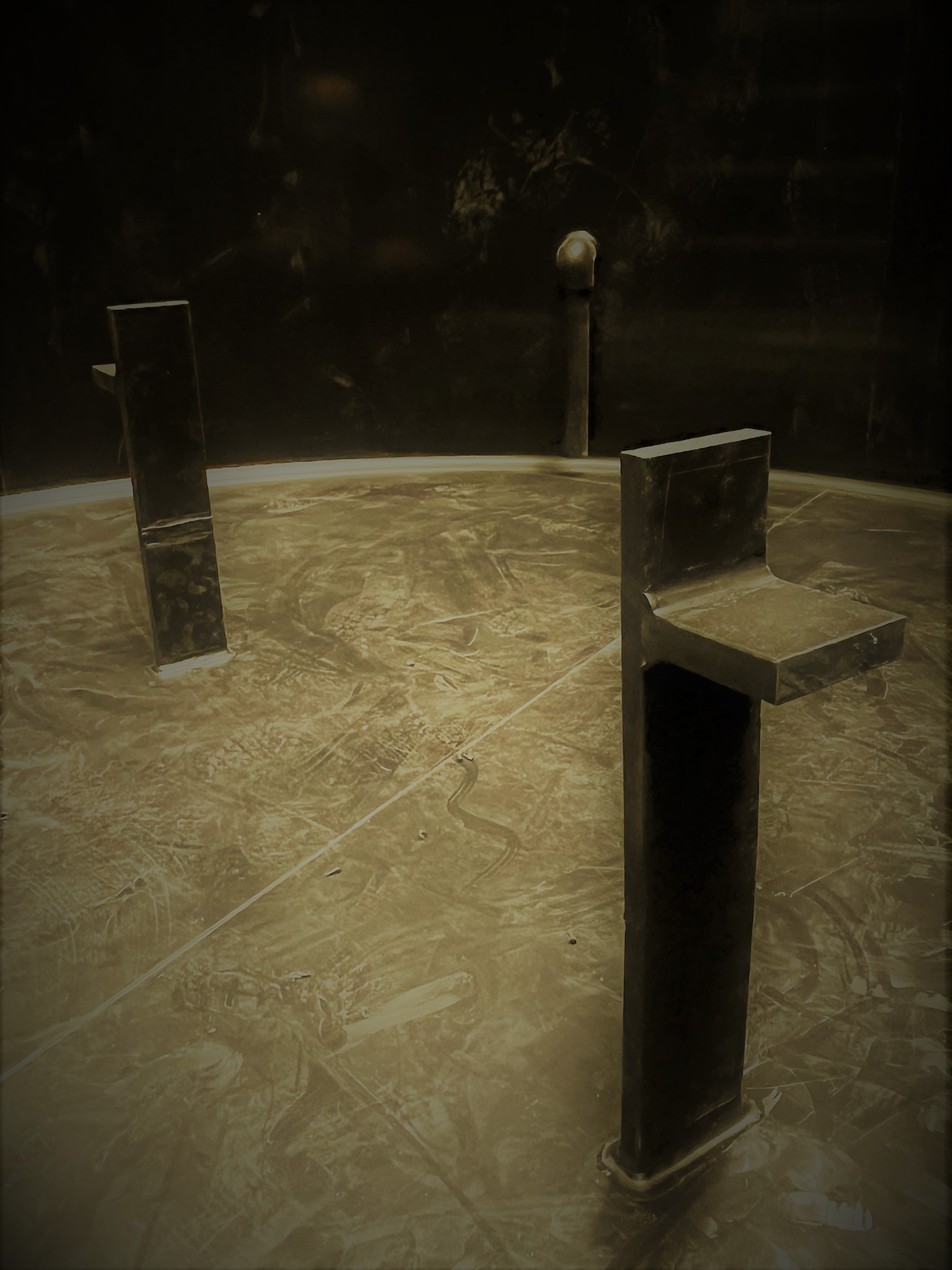
Baza wiedzy
Co wiesz o rewizjach zbiorników dozorowych i wydłużeniu okresu ich żywotności?
Zbiorniki podlegające dozorowi technicznemu wymagają okresowych rewizji – zewnętrznych i wewnętrznych. Znacznym ułatwieniem w realizacji procesu są unikalne elementy wskaźnikowe montowane w każdym nowo produkowanym zbiorniku dozorowym.
W artykule omawiamy ww. rewizje i sposoby na ocenę stanu konstrukcji mającą wpływ na decyzję o wydłużeniu okresu żywotności.
Izolacja konstrukcji zbiornika
Projektując konstrukcję zbiornika, dobiera się rodzaj izolacji, która ma zapewnić wymagane parametry pracy w panujących warunkach otoczenia. Służy także utrzymaniu prawidłowych właściwości fizyczno-chemicznych przechowywanego czynnika. Niektóre media należy chronić przed wystygnięciem – spadkiem temperatury (na przykład ług sodowy), a inne odwrotnie – przed wzrostem temperatury, gdyż ulegają rozpadowi lub tracą swe właściwości – na przykład podchloryn sodu czy woda utleniona.
Pierwszym sposobem ochrony termicznej zbiorników jest izolacja powszechnie znaną wełną mineralną. Okłada się nią zarówno cylinder, jak i dach zbiornika. W przypadku zbiorników zewnętrznych, które pracują w skrajnych warunkach temperaturowych, czyli na przykład −20°C, izoluje się także dno.
Izolację wykonuje się szczególnie dla konstrukcji z polipropylenu PP lub poli(chlorku winylu) PVC, który jest dość kruchy i podatny na uszkodzenia w przypadku spadków temperatury. Zależnie od warunków izolacją mogą zostać objęte także rurociągi przesyłowe, które transportują medium ze zbiornika na dalszą część instalacji.
W przypadku zastosowania wełny mineralnej zbiornik ma konstrukcję dwupłaszczową. Wewnątrz znajduje się cylinder właściwy, następnie montowana jest izolacja i całość zamyka się płaszczem ochronnym. Płaszcz zewnętrzny wykonuje się z płyty polietylenowej, polipropylenowej lub blachy aluminiowej.
Do ocieplenia zbiorników stosuje się także piankę poliuretanową (PUR). Nie jest to jednak powszechne rozwiązanie.
Należy pamiętać, że w przypadku zbiorników magazynowych, które podlegają dozorowi Urzędu Dozoru Technicznego i które obligatoryjnie są wyposażane w wannę wychwytową, ocieplenie obejmuje tylko zbiornik główny przechowujący medium, nie zaś wannę.
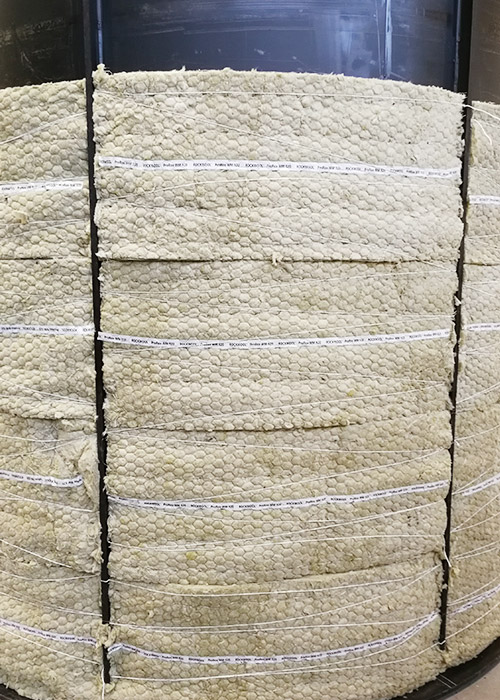
Montaż izolacji na zbiorniku magazynowym – wełna mineralna połączona z jednostronną okładziną z siatki galwanizowanej.
Widok w przybliżeniu na wełnę z siatką galwanizowaną, która nadaje materiałowi izolacyjnemu sztywność.
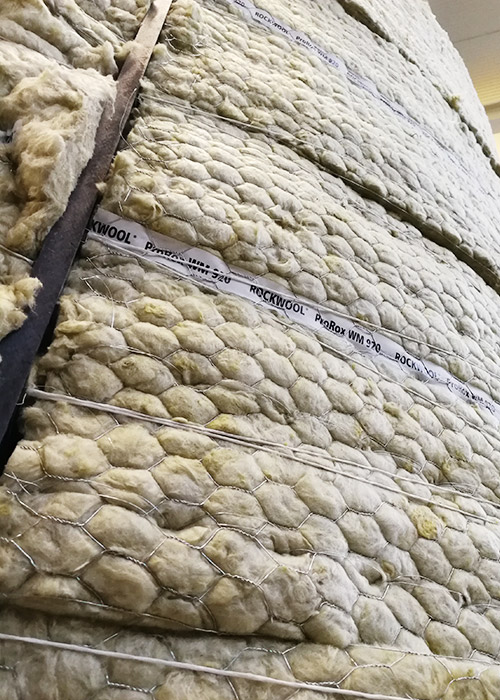
Instalacja grzewcza jako ochrona przed zmianą właściwości fizykochemicznych medium
W zależności od rodzaju substancji i wymaganych parametrów procesu dla zbiorników chemoodpornych dodatkowo projektuje się instalację grzewczą. Ma ona na celu na przykład ochronę czynników roboczych przed utratą właściwości fizykochemicznych. Szczególne zastosowanie znajduje w przypadku magazynowania stężonego ługu sodowego, który poniżej temperatury 20°C może krystalizować. Aby zapewnić ciągłość procesu i nie doprowadzić do przestojów w sytuacji awarii, zbiorniki magazynowe wyposaża się w systemy redundantne, czyli zdublowane.
Ochrona przed wyciekiem substancji trujących, żrących i ciekłych zapalnych
W przypadku magazynowania substancji trujących, żracych i ciekłych zapalnych, czyli dla zbiorników podlegających dozorowi technicznemu, konieczne jest zastosowanie zabezpieczenia przed wyciekiem medium. Formy takiej ochrony reguluje rozporządzenie Ministra Gospodarki z dnia 16 kwietnia 2002 r. [1] oraz z dnia 18 września 2001 r. [2].
Rozporządzenie określa, że wykonanie odrębnego zabezpieczenia przed przenikaniem czynnika roboczego do gruntu oraz do wód powierzchniowych i gruntowych należy przewidzieć w przypadkach, gdy pojemność zbiornika na ciecze żrące i bardzo toksyczne przekracza 1 m3, czyli już od stosunkowo małych zbiorników (w przemyśle na ogół stosuje się znacznie większe pojemności, rzędu kilkunastu, kilkudziesięciu metrów sześciennych), a największy zainstalowany w Polsce zbiornik z laminatu ma pojemność aż 1150 m³.
Urządzenia chroniące przed wyciekiem według § 11 ust. 2 rozporządzenia [1]:
- podwójna ścianka zbiornika i monitorowanie przestrzeni międzyściankowej,
- zbiornik rezerwowy, ściana osłonowa, obwałowanie lub taca,
- hermetyczne pomieszczenie z drzwiami umiejscowionymi na odpowiedniej wysokości, w którym jest ustawiony zbiornik,
- geomembrana.
W praktyce najczęściej projektowanym rozwiązaniem jest tzw. konstrukcja dwupłaszczowa, w której drugi płaszcz pełni funkcję wanny wychwytującej. Projektuje się także zbiorniki stojące w wannie zabezpieczająco-wychwytującej. W przypadku baterii zbiorników przewiduje się albo jedną wannę dla wszystkich, albo odrębne dla każdego ze zbiorników. Pojemność takiej wanny oblicza się według wytycznych zapisanych w rozporządzeniu [1].
W zależności od technologii produkcji w zbiornikach Amargo®, jako inny rodzaj zabezpieczenia, projektowany jest także płaszcz z systemem monitorowania szczelności. Stosowany jest dla zbiorników wykonywanych technologią nawojową, z systemem dwuściennym, nazywaną wewnętrznie AmargTank MultiLayer DoubleWall®. Konstrukcja ta daje możliwość monitorowania części międzywarstwowej zbiornika, umożliwiając aplikację w przestrzeni międzyściankowej tworzywa systemu nad- lub podciśnieniowego monitoringu detekcji wycieków. Daje to możliwość precyzyjnego pomiaru zmian ciśnienia pomiędzy obiema płaszczyznami zbiornika: wewnętrzną i zewnętrzną.
Zabezpieczenia ochronne zbiornika wskazane przez rozporządzenia [1] i [2] są obligatoryjne dla zbiorników podlegających dozorowi technicznemu. W innych przypadkach sposób zabezpieczenia normują przepisy BHP oraz warunki panujące w danym zakładzie przemysłowym. Dobierane jest wówczas optymalne technicznie i ekonomicznie rozwiązanie zabezpieczające w formie tacy wychwytującej o wymaganej pojemności roboczej.
Technologie monitorowania stanu zbiornika
Systemy zbierania i analizowania danych w czasie rzeczywistym pozwalają na precyzyjną analizę stanu zbiornika w całym cyklu życia. Przewidywanie uszkodzeń, deformacji czy pęknięć umożliwia podejmowanie decyzji o możliwości dalszej bezpiecznej eksploatacji zbiornika lub wycofaniu go z użytkowania. Systemy służą poprawie parametrów projektowanych zbiorników i stworzeniu realnego cyfrowego bliźniaka danego zbiornika.
Podczas pracy monitorowane są parametry pracy, tj. temperatura medium na dolocie i w zbiorniku, temperatura otoczenia, nadciśnienie, poziom napełnienia. Porównywane są z tymi przyjętymi na etapie doboru konstrukcji i projektowania. Dodatkowo wprowadzane są czujniki pomiaru zmian parametrów struktury ścianek w trakcie lat eksploatacji, tj. czujniki piezoelektryczne, światłowodowe lub tensometry.
Projektowanie kompletnych instalacji towarzyszących
Poza zbiornikiem i zabezpieczeniem przed wyciekiem w projekcie uwzględnia się niejednokrotnie instalacje towarzyszące wraz z podpięciem zbiorników do całego układu i rozruchem.
- Instalacje przesyłowe – od stanowisk UNO po zbiornik
- Instalacje dozujące – od zbiornika dozującego na instalację
- Wentylacja oraz hermetyzacja oparów (dodatkowe zawory napowietrzająco-odpowietrzające zapewniające stabilność pracy urządzenia)
- Stacje NO wraz z odbiorem z odbiorem Transportowego Dozoru Technicznego
- Okablowanie, automatyka i sterowanie, IOT, przesył danych i spięcie z systemami w zakładzie przemysłowym
Zależnie od rodzajów cystern i metod rozładunku należy mieć więc na względzie dalszy ciąg instalacji. W zbiornikach magazynowych dozorowych według rozporządzenia [1] podciśnienie musi wynosić jedynie 0,0025 bara, a nadciśnienie 0,035 bara, jest to więc wąski przedział. Na etapie projektowania należy przewidzieć urządzenia na ciągu rurociągów między stanowiskiem NO a zbiornikiem, które zapewnią nieprzekraczanie tych zakresów.
Jest to szczególnie ważne w przypadku rozładunku sprężonym powietrzem, podczas którego może dojść do niebezpiecznej sytuacji, gdy cysterna jest rozładowywana praktycznie do zera, po czym może nastąpić uderzenie sprężonego powietrza na instalacje i zbiorniki. Należy przewidzieć urządzenia, które zapobiegną temu uderzeniu, lub stosować rozładunek przy użyciu pomp, przy którym mamy większą kontrolę nad procesem. Analogicznie jak dla zbiorników transportowych, zbiorniki magazynowe także wyposaża się w czujniki przepełnienia z wizualizacją stopnia napełnienia widoczną dla operatora.
Proces projektowania zarówno stanowisk NO, jak i zbiorników magazynowych i instalacji powinien być prowadzony kompleksowo.
W przypadku zbiorników magazynowych dozorowych projekt zawsze należy uzgodnić z Urzędem Dozoru Technicznego. Dopiero wtedy można rozpocząć produkcję zbiornika. Jeśli po takim uzgodnieniu będą wprowadzane zmiany dotyczące na przykład gabarytu lub choćby konfiguracji króćców (średnic, rozmieszczenia), konieczne będzie ponowne uzgodnienie.
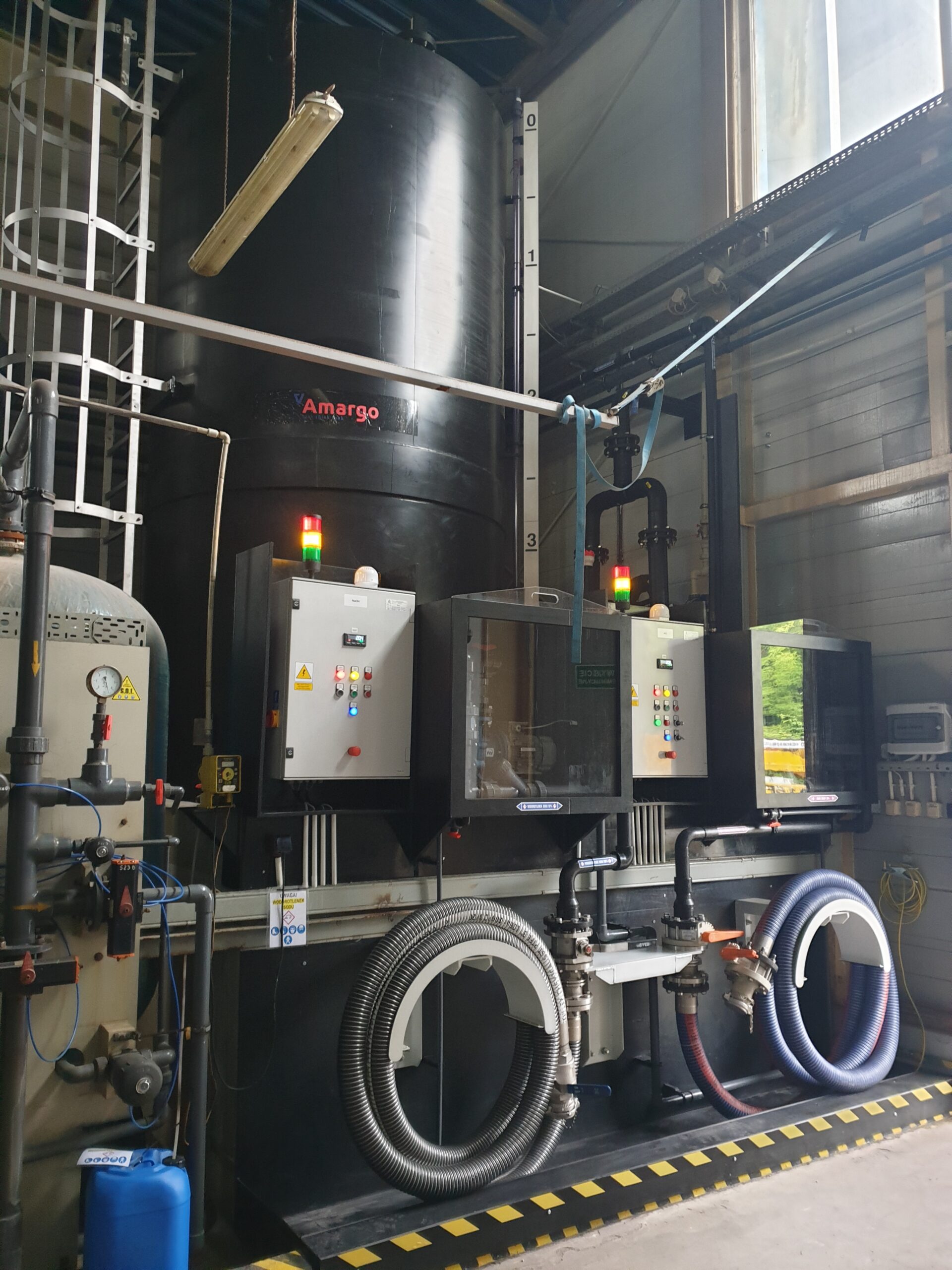
Widok na instalację wewnątrz budynku: dozorowy zbiornik magazynowy ługu sodowego NaOH oraz stacje rozładunkowe dla zbiornika NaOH oraz zbiornika na HCl znajdującego się na zewnątrz obiektu.
Instalacja tankowania zbiornika z obudową i wanną wychwytową szczelną na ewentualne wycieki wyposażona w zawór odwadniający obudowę, dodatkowo szafa pomocnicza układu AKiP.
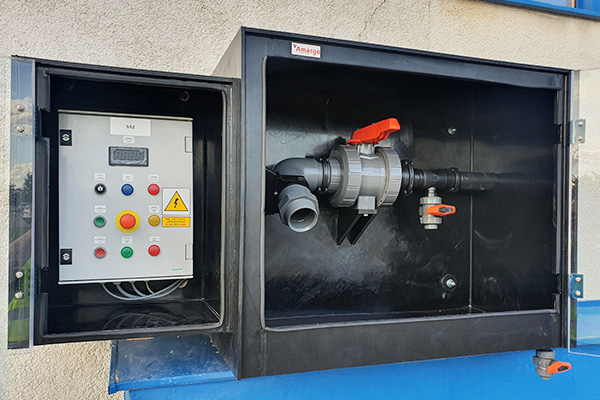
Wiedza o zbiornikach, szczególnie na chemikalia, jest specjalistyczna, a dobór właściwych rozwiązań jest niezwykle ważny już na wczesnych etapach projektu. To pozwala uniknąć podstawowych błędów. Dlatego też proces projektowania powinien być poprzedzony audytem, którego celem jest analiza i ocena potencjału oraz możliwości realizacji inwestycji, z uwzględnieniem specyfiki procesu technologicznego.
Na podstawie wyników audytu inżynierowie opracowują koncepcję wdrożenia, w której rekomendowane są optymalne rozwiązania techniczne. Koncepcja uwzględnia poznane potrzeby, a także możliwości finansowe oraz logistyczne. Dopiero wtedy można przejść do opracowania projektu i obliczeń statyki zbiornika na bazie wybranego wariantu rozwiązania. Taką ścieżkę postępowania rekomendujemy i z powodzeniem realizujemy we współpracy z naszymi Klientami.
Literatura:
- Rozporządzenie Ministra Gospodarki z dnia 16 kwietnia 2002 r. w sprawie warunków technicznych dozoru technicznego, jakim powinny odpowiadać zbiorniki bezciśnieniowe i niskociśnieniowe przeznaczone do magazynowania materiałów trujących lub żrących, Dz.U. z 2002 r. Nr 63, poz. 572.
- Rozporządzenie Ministra Gospodarki z dnia 18 września 2001 r. w sprawie warunków technicznych dozoru technicznego, jakim powinny odpowiadać zbiorniki bezciśnieniowe i niskociśnieniowe przeznaczone do magazynowania materiałów ciekłych zapalnych, Dz.U. z 2001 r. Nr 113, poz. 1211.
- PN-EN 12573-2:2004 – Spawane stacjonarne bezciśnieniowe zbiorniki termoplastyczne – Część 2: Obliczanie pionowych zbiorników cylindrycznych.
- DVS 2205 – Calculation of tanks and apparatus made of thermoplastics (Obliczenia dla aparatury i zbiorników z tworzyw termoplastycznych)
Porozmawiajmy o rozwiązaniu Twojego wyzwania
Rozmowa to klucz do sukcesu. Skorzystaj z naszej wiedzy i doświadczenia.