Jak zamontować wielkogabarytowy zbiornik przemysłowy w trudno dostępnej hali bez ingerencji w istniejącą infrastrukturę?
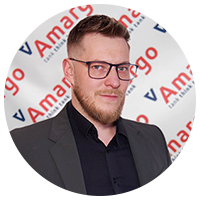
Grzegorz Zając, Ekspert z zakresu zbiorników i instalacji przemysłowych z tworzyw sztucznych
W wielu zakładach przemysłowych modernizacja infrastruktury wiąże się z poważnymi wyzwaniami logistycznymi. Co zrobić, gdy nowy zbiornik o dużych gabarytach musi zostać zamontowany w istniejącej hali, a dostępne wejście jest zbyt małe, by wprowadzić go w całości? Jak zapewnić bezpieczeństwo prac montażowych w ograniczonej przestrzeni? Z takim właśnie problemem zmierzyło się jedno z przedsiębiorstw energetyki cieplnej.
Klient rozpoczął rozmowy z Amargo® w momencie, gdy projekt znajdował się na etapie opracowywania koncepcji modernizacji stacji przygotowania wody, w ramach której jednym z kluczowych elementów miała być wymiana zbiornika wody demineralizowanej.
Już na początku przedsiębiorstwo zasygnalizowało ograniczenia przestrzenne i brak pełnych danych projektowych. W trakcie pierwszych rozmów w miejscu planowanej inwestycji znajdował się bowiem stary zbiornik, który zajmował przestrzeń przeznaczoną pod nową konstrukcję. Do czasu jego demontażu precyzyjne określenie dopuszczalnej średnicy konstrukcji zamiennej było niemożliwe.
Zamiast sztywnej wyceny potrzebne było techniczne wsparcie i audyt na miejscu. Klient zdecydował się zaufać naszemu zespołowi i po demontażu zbiornika zaprosił nas na wizję lokalną, traktując ją jako kluczowy etap przygotowań do inwestycji. Był to również sposób na wcześniejsze zidentyfikowanie potencjalnych problemów realizacyjnych.
Największym wyzwaniem był dostęp do hali – jedyną możliwą drogą transportową były drzwi przemysłowe o szerokości 1,1 m i wysokości 6 m. Nowy zbiornik miał mieć pojemność 60 m³ i wysokość rzędu 9 m, a dostępny otwór stropowy (3,3 m) nie mógł być poszerzany – inwestor wykluczył ingerencję w infrastrukturę budynku.
Istniejące ograniczenia logistyczne i architektoniczne znacząco wpływały na proces wymiany zbiornika.
Operacja „zbiornik”: jak zamieniliśmy logistyczny problem w konstrukcyjny sukces
Kiedy podczas wizji lokalnej po raz pierwszy stanęliśmy przed halą produkcyjną zakładu, od razu stało się jasne, że standardowe podejście nie wchodzi w grę.
Nie rozłożyliśmy jednak rąk. Nie padła też z naszej strony ani sugestia zmiany lokalizacji, ani propozycja kosztownej przebudowy. Zamiast tego postawiliśmy na elastyczność, doświadczenie i innowacyjność – wartości, które tworzą DNA Amargo® jako tank think tanku.
Po dokładnej analizie warunków, zaproponowaliśmy niestandardowe rozwiązanie: nowy zbiornik wody DEMI miał powstać z pojedynczych segmentów, które można było złożyć ze sobą niczym konstrukcję z klocków. Kluczowym elementem planu było więc zaprojektowanie całego zbiornika z uwzględnieniem mniejszych modułów, możliwych do wniesienia pojedynczo przez drzwi przemysłowe, a następnie ich precyzyjne zmontowanie bezpośrednio na miejscu – bez utraty wytrzymałości czy szczelności.
Nie było to jednak tak proste, jak mogłoby się wydawać na pierwszy rzut oka. Takie podejście wymagało szczegółowych obliczeń statycznych, które przedstawiliśmy Klientowi, aby potwierdzić, że proponowana konstrukcja będzie bezpieczna i trwała przez długie lata użytkowania w określonych warunkach.
Obliczenia statyki zostały zaprezentowane „na żywo”, krok po kroku, z użyciem specjalistycznego oprogramowania. Dzięki temu Klient miał okazję przekonać się, jak duże znaczenie mają dobrze przeprowadzone obliczenia inżynierskie. To doświadczenie uświadomiło mu, jak istotne jest, aby konstrukcja była oparta na rzetelnej analizie technicznej — i jak łatwo można przeoczyć ten aspekt, jeśli się go nie zweryfikuje.
W efekcie spotkania Klient uzyskał konkretne dane i argumenty dotyczące m.in. grubości ścianek, wysokości zbiornika i innych parametrów wpływających na końcowy koszt i bezpieczeństwo inwestycji, co pozwoliło mu podjąć świadomą decyzję i zwiększyło pewność co do powodzenia całego przedsięwzięcia.
Dodatkowo zadanie wymagało skrupulatnego planu logistycznego, który umożliwił płynne dostawy i montaż bez zakłócania codziennej pracy zakładu. Ważną rolę odegrała także wyspecjalizowana ekipa montażowa, która musiała pracować w dość nietypowych warunkach.
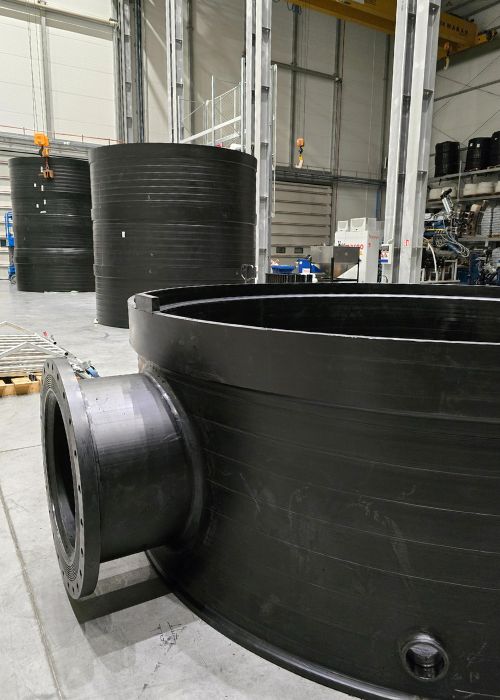
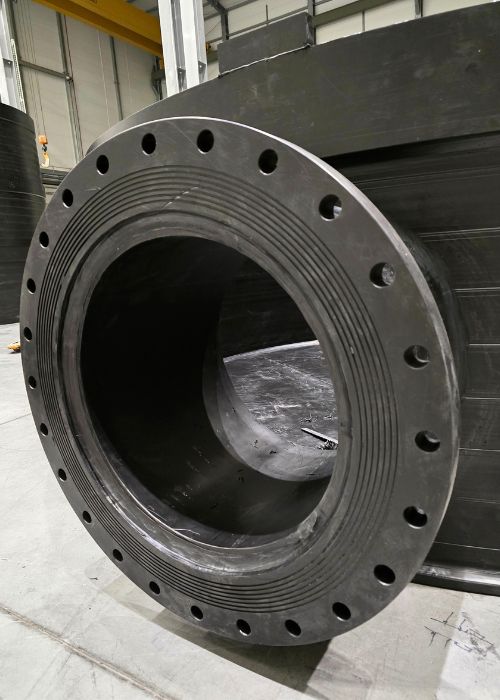
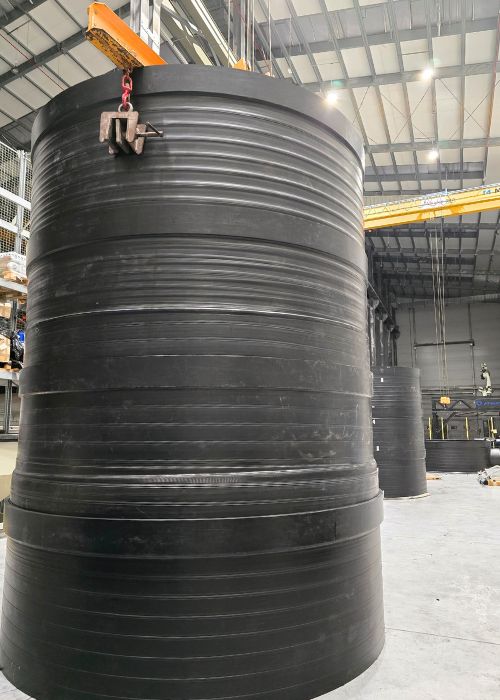
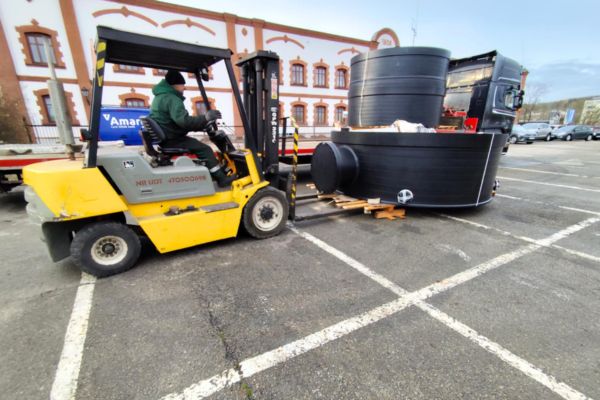
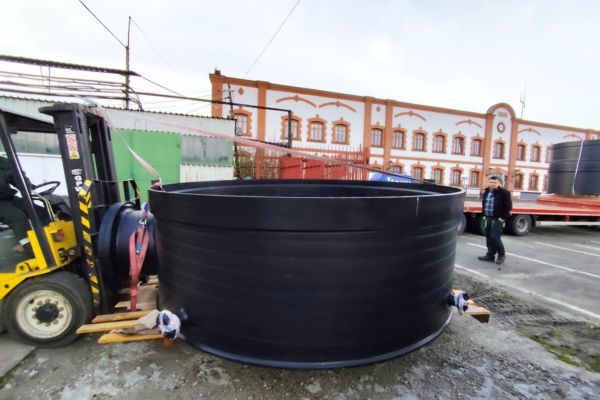
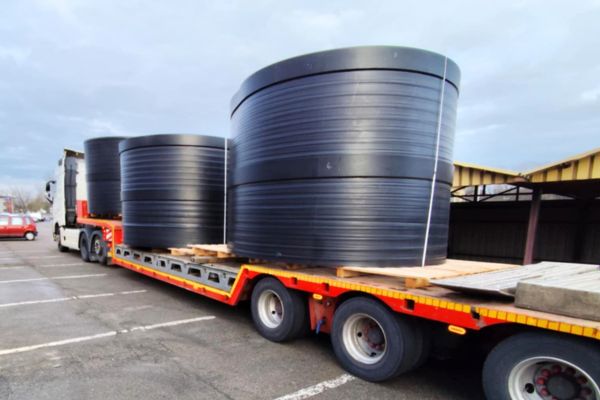
Produkcja i montaż – sprawdzian dla inżynierii
Zbiornik na wodę demineralizowaną został zaprojektowany i wykonany z tworzywa klasy PE100, o 20-letniej żywotności. Dziewięć cylindrycznych segmentów wytworzono w zakładzie Amargo® w technologii nawojowej AmargTank SafeSeamLess® – polegającej na nawijaniu ekstrudowanej wstęgi PE100 na stalową formę, a następnie rozformowaniu i obróbce segmentów. Osobno wykonano i zespawano mufy łączące.
Poszczególne segmenty były sukcesywnie wnoszone do wnętrza hali. Obserwująca to z zainteresowaniem ekipa klienta – z początku pełna rezerwy – z każdą minutą zyskiwała pewność, że rozwiązanie się sprawdzi.
Najtrudniejszym etapem był montaż segmentów-cylindrów zbiornika w ograniczonej przestrzeni roboczej. Spawanie ekstruzyjne wymagało precyzji i pełnej synchronizacji działań. Najwięcej emocji towarzyszyło osadzeniu ostatniego segmentu – operacja zakończyła się sukcesem.
Dach i podłogę zbiornika wykonano z płyt PE100, a następnie trwale połączono z cylindrycznym płaszczem metodą spawania ekstruzyjnego (dach – od strony zewnętrznej).
Cała konstrukcja o wymiarach Ø 3 m i wysokości ok. 9 m została posadowiona na wcześniej przygotowanym fundamencie.
Dzięki ścisłemu planowaniu logistycznemu i precyzyjnej koordynacji zespołu montażowego, prace odbywały się bez zakłócania bieżącego funkcjonowania zakładu – co było kluczowe z perspektywy działu utrzymania ruchu.
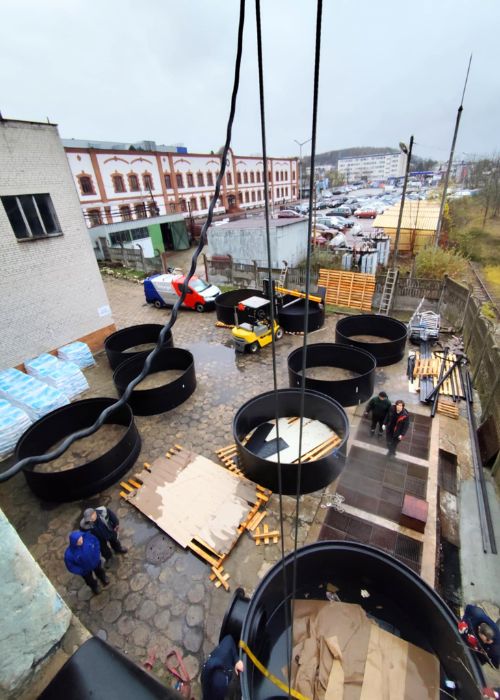
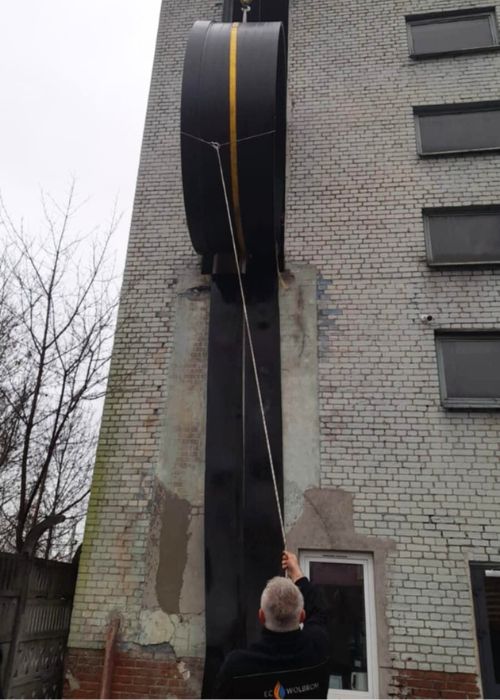
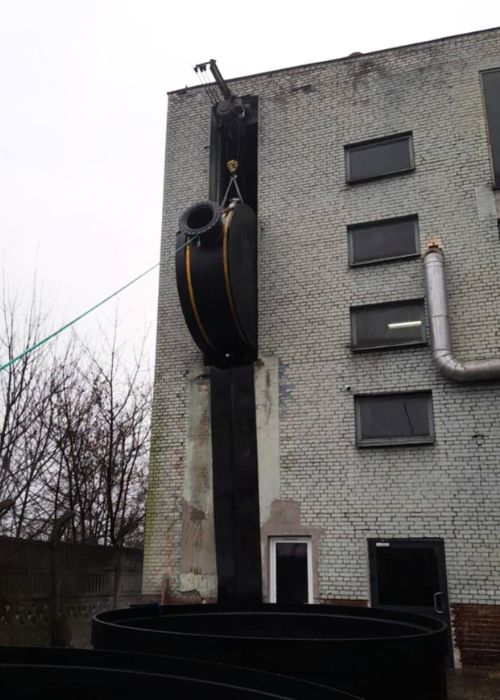
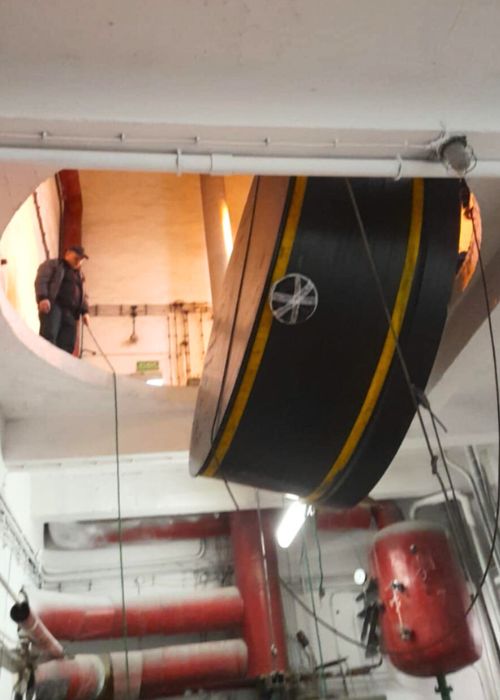
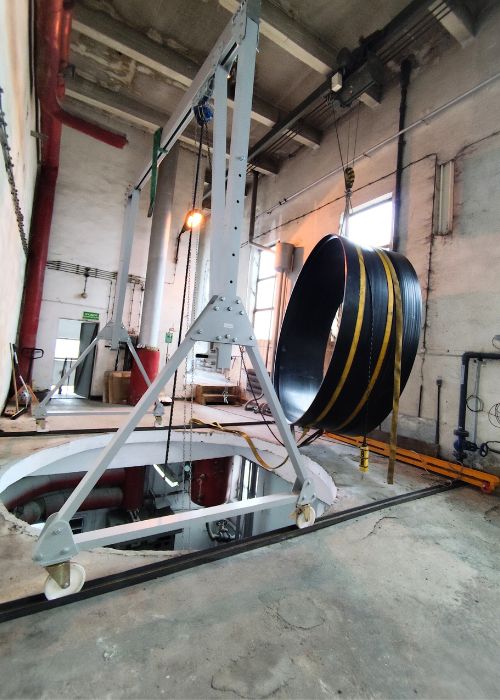
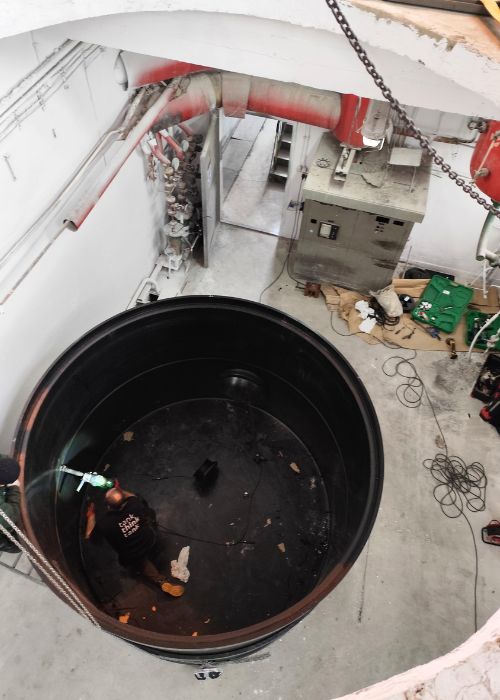
Wnioski z realizacji wielkogabarytowego zbiornika przemysłowego – dla zespołów technicznych, UR, działów BHP
Z tej złożonej i nietypowej realizacji wynikają istotne wnioski dla działów technicznych, utrzymania ruchu oraz BHP. Przede wszystkim – ingerencja w strukturę budynku nie zawsze jest konieczna. Warto w takich sytuacjach skorzystać z doświadczenia wytwórców zbiorników przemysłowych, szczególnie tych, którzy oferują niestandardowe podejścia oraz wsparcie w postaci audytów czy wizyt referencyjnych w innych zakładach.
Nie do przecenienia jest również kwestia bezpieczeństwa. Wielkogabarytowe zbiorniki wymagają precyzyjnych projektów oraz obliczeń statycznych. Kluczowe znaczenie ma tu wybór producenta, który dysponuje właściwym zapleczem technologicznym oraz przestrzega zasad projektowych, takich jak minimalny promień gięcia płyt uzależniony od ich grubości.
Niestosowanie się do tych wymogów przez konkurujące w procesie inwestycyjnym firmy – np. poprzez zwijanie cylindrów z płyt w sposób powodujący nadmierne naprężenia – mogło skutkować powstawaniem spękań naprężeniowych, efektem karbu i w konsekwencji awarią konstrukcji.
Amargo®, jako wytwórca dysponujący technologią nawojową – beznaprężeniową metodą produkcji cylindrów i zbiorników – umożliwia realizację konstrukcji o dużych pojemnościach. Rozwiązanie to zapewnia większą swobodę projektową i jednocześnie minimalizuje ryzyko defektów materiałowych.
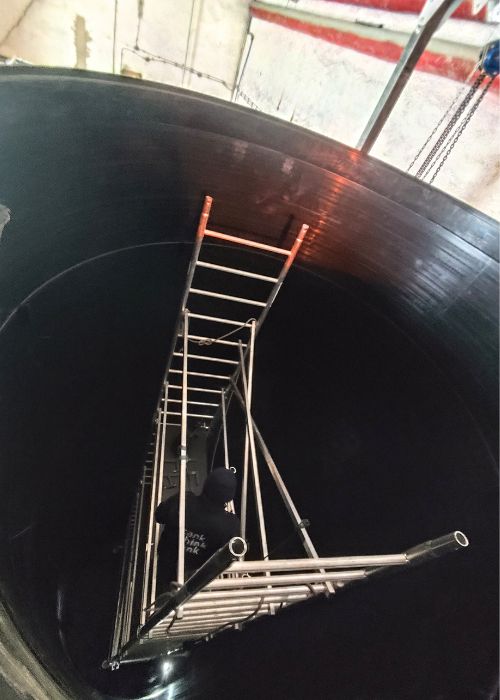
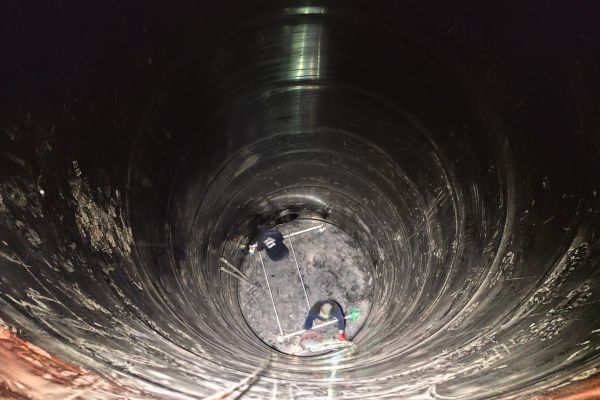
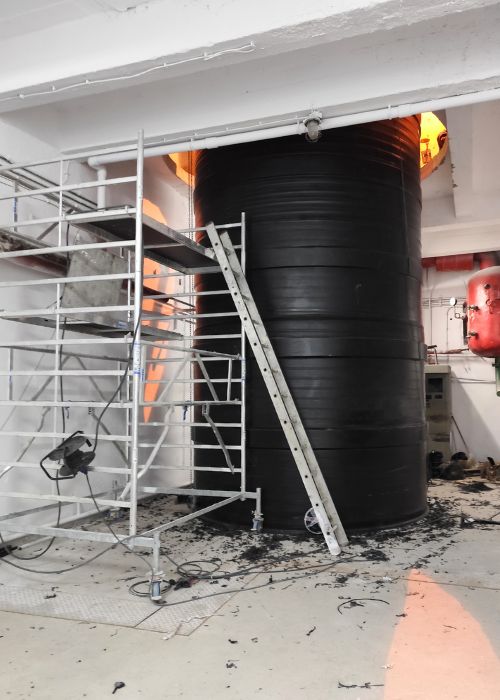
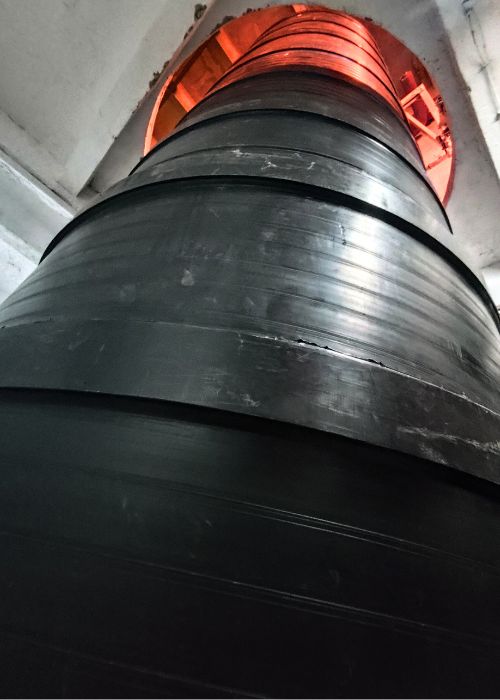
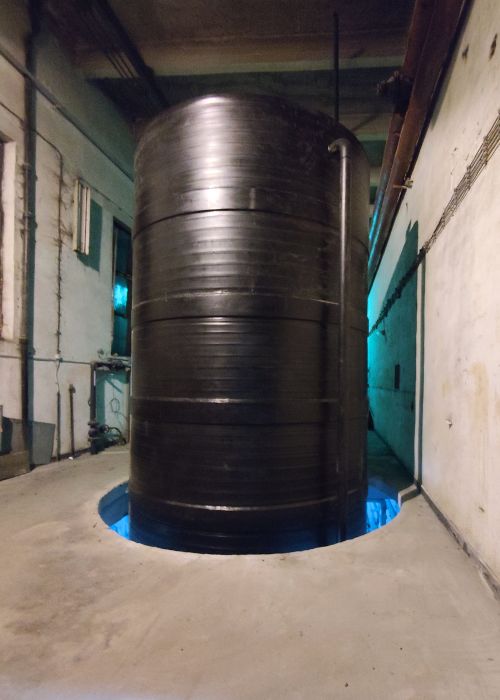
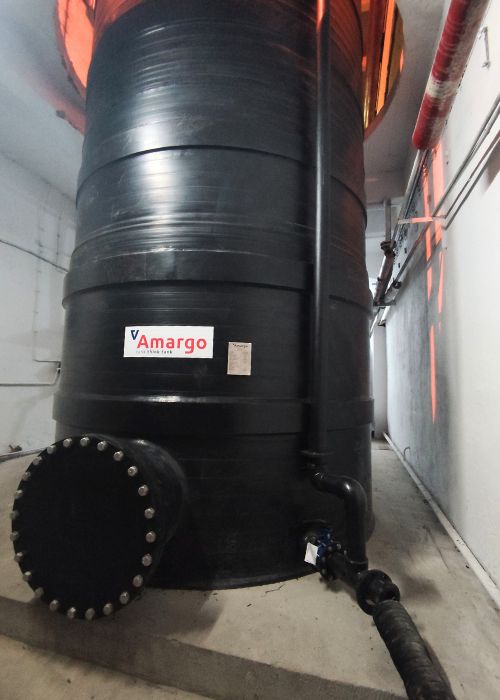
Takie kompleksowe podejście, oparte na precyzyjnym planowaniu logistycznym oraz inżynieryjnym know-how, umożliwia skuteczną realizację inwestycji nawet w bardzo trudnych warunkach przestrzennych.
Projekt ten stanowi przykład partnerskiej współpracy obejmującej pełen cykl realizacyjny – od audytu/koncepcji, przez projekt i produkcję, aż po transport i montaż.
Porozmawiajmy o rozwiązaniu Twojego wyzwania
Rozmowa to klucz do sukcesu. Skorzystaj z naszej wiedzy i doświadczenia.