Wielkogabarytowe zbiorniki w przemyśle służą do bezpiecznego przechowywania tak zwanych czynników roboczych: substancje chemicznych, nierzadko substancji żrących, wody rezerwowej czy wody do zasilania instalacji i sieci przeciwpożarowych. Te ciecze są niezbędne do niezawodnego i bezpiecznego prowadzenia procesów produkcyjnych. Żeby pokazać jak powstają takie zbiorniki, zapraszamy do obejrzenia wideo z naszego zakładu produkcyjnego.
Pierwszy rekomendowany krok, czyli audyt i koncepcja
Czy jest jedna właściwa, niezmienna ścieżka postępowania w przypadku inwestycji w zbiorniki i instalacje chemoodporne? Można uznać, że nie ma na to gotowej recepty. Każda sytuacja jest inna i wyjątkowa, każdy problem ma swoje źródło, każde przedsiębiorstwo realizuje inwestycje według ustalonych reguł, każde ma inne możliwości finansowe czy logistyczne…
Ale… Jako że z powodzeniem realizujemy inwestycje w modelu zaprojektuj i wybuduj, rekomendujemy pewną ścieżkę, jaką podążamy we współpracy z naszymi Klientami. Pewnych kroków nie warto pomijać, bo dzięki nim możemy dojść po przysłowiowej nitce do kłębka, spojrzeć na problem holistycznie, dobrać optymalne rozwiązania, zadbać o to, by instalacje działały kompletnie, w sposób bezpieczny i pewny przez wiele kolejnych lat.
Dlaczego o tym wspominamy? Bo warto zacząć od konsultacji i koncepcji, która często jest niedoceniana, a co za tym idzie – pomijana. Skraca się ten proces, co na finale może skutkować tym, że w założeniach są luki powstałe na skutek np. braku świadomości o potencjalnych ryzykach i konsekwencjach, jakie mogą pojawić się podczas prowadzonych prac i które mogą rzutować nie tylko na bezpieczeństwo, ale też czas realizacji i jej finalne koszty. To czasami może nawet przesądzić o realizacji.
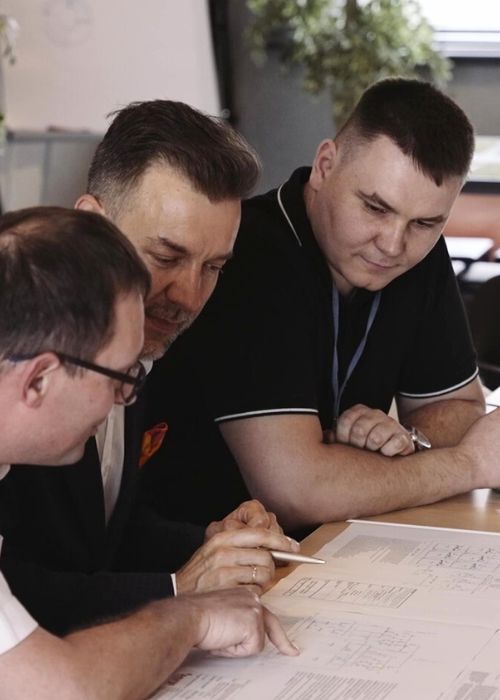
Konsultacje, audyt przemysłowy, koncepcja wdrożenia
Skorzystaj z doradztwa naszych ekspertów
Nie wahaj się skorzystać z doradztwa, dzięki któremu otrzymasz kompleksowe wsparcie na etapie przygotowania do inwestycji: ocenimy Twój problem, dokonamy analizy możliwych rozwiązań, pomożemy Ci zorientować się w kosztach i wskażemy właściwą drogę postępowania.
Opracowanie projektu
Projekt często jest tym pierwszym, namacalnym etapem. Powstaje on jednak na bazie wcześniejszych konsultacji i audytu. Projekt uwzględnia warunki w jakich zbiornik będzie użytkowany, przede wszystkim jakie medium będzie w nim przechowywane. Inżynierowie – technologowie obliczają grubość ścianek, dobierają materiały i wskazują proces wykonania: tradycyjne zwijanie i zgrzewanie lub technologię nawojową. W przypadku zbiorników dozorowych projekt jest jeszcze uzgadniany z jednostką Urzędu Dozoru Technicznego UDT.
Technologia tradycyjna, czyli AmargTank ClassicWeld®
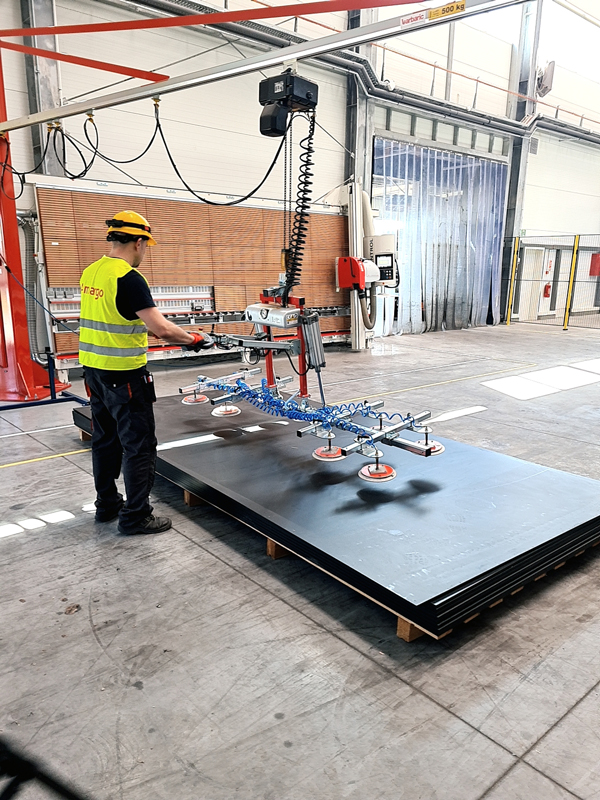
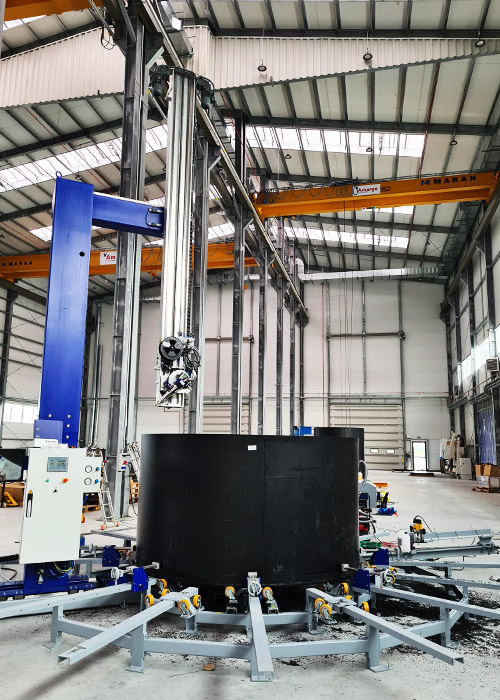

Technologia tradycyjna, czyli AmargTank ClassicWeld® polega na wykorzystaniu półproduktów z arkuszami tworzywa sztucznego. Materiał ich wykonania to głównie polietylen klasy PE100 i polipropylen PP. W naszym magazynie gromadzone są również pozostałe elementy zbiorników, czyli różnego rodzaju króćce, włazy, drabinki, bariery, pomosty, zawory oraz pompy.
Produkcja rozpoczyna się od odpowiedniego przycięcia arkusza tworzywa. Pobierany jest on manipulatorem z magazynu i stawiany pionowo na 6-metrowej pile. Cięcie rozpoczyna się po uruchomieniu na komputerze odpowiedniego programu.
Następnie formatka trafia na stanowisko obróbki CNC, czyli plotera tnąco-frezującego. Głównym narzędziem maszyny jest wrzeciono wysokoobrotowe, ale posiada ono też magazynek, z którego automatycznie pobiera potrzebne frezy. Wycina się tu poszczególne części zbiornika, otwory oraz wykonuje np. listwy wskaźnikowe.
Elementy, które mają zostać połączone trafiają pod miecz zgrzewarki. Gdy znajdą się one na stole, wysuwa się teflonowany miecz rozgrzany do temperatury 220°C. Zapewnia on pełne połączenie łańcuchów polimerowych obu elementów w czasie od 5 minut do 2 godzin.
Zgrzane arkusze trzeba zespawać. Służy do tego drut spawalniczy, który powstaje w specjalnej maszynie. Do zasobnika wsypuje się granulat, a urządzenie uplastycznia go i wytłacza gorący drut o różnych przekrojach. Po ostygnięciu zwijany jest na rolki.
Jak przebiega maszynowe spawanie dna zbiornika? Najpierw cylinder, dno i dach prowizorycznie łączy się urządzeniem typu hot gas. Następnie ekstruder wciąga drut spawalniczy z rolek, podgrzewa go i wytłacza powstałą w ten sposób masę termoplastyczną. Formowana jest za pomocą buta spawalniczego, który trwale łączy elementy na automatycznie obracającym się stole.
Kolejny etap przebiega na zrobotyzowanym stanowisku spawalniczym. Robot o zasięgu ramienia do 3,5 metra dysponuje spawarką przygotowaną do pracy ciągłej oraz wymiennymi urządzeniami peryferyjnymi.
Na stanowisku wykończeniowym montuje się żebra centrujące zbiornik w wannie zabezpieczającej. Instaluje się tu także wsporniki pod drabiny, podesty, pomosty oraz inne detale.
Na koniec zbiorniki poddawane są próbie szczelności lub ciśnieniowej. W przypadku zbiorników dozorowych jeśli inspektorzy dozoru technicznego nie mają zastrzeżeń, zbiorniki mogą jechać do miejsca przeznaczenia.
Technologia nawojowa, czyli AmargTank SafeSeamLess®, MultiLayer® oraz MultiLayer DoubleWall®
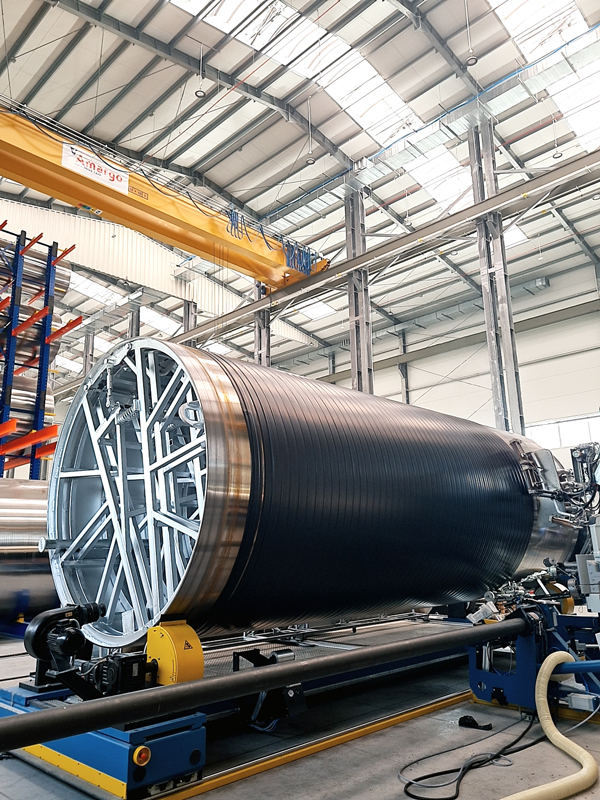
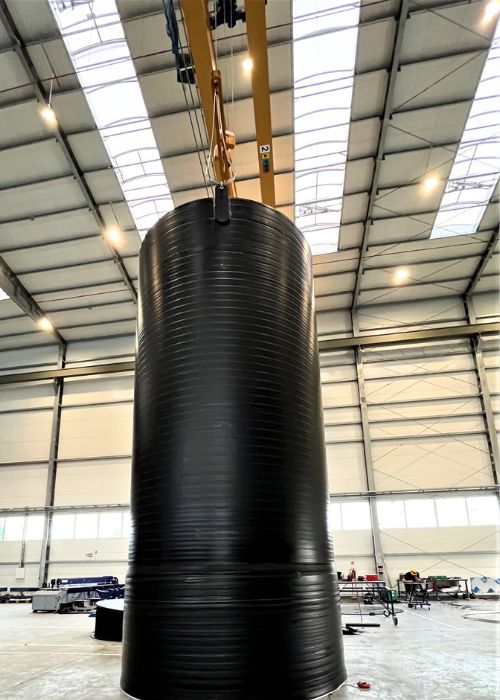
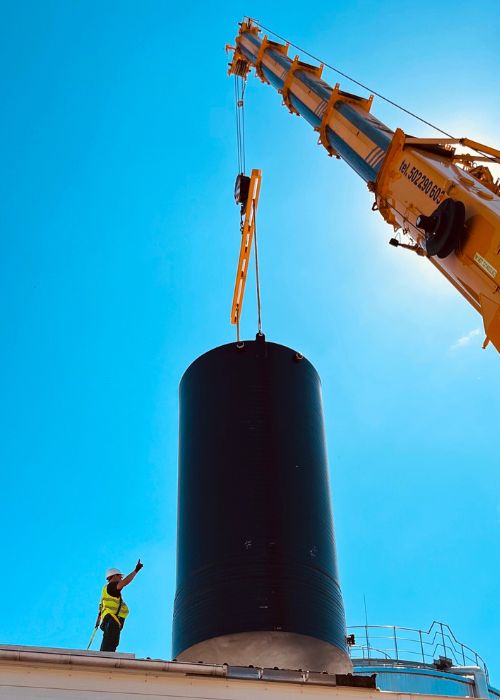
W technologii nawojowej powstają zbiorniki, których nie da się zrobić z użyciem płyt: np. wysokie i o małej średnicy. Wykorzystuje się w tym celu tak zwany granulat pierwotny, który zostaje pobrany z magazynu, wsypany do zasobników i przekazany przez pompę próżniową do dwóch ekstruderów dysponujących stalowymi walcami o średnicy do 4 m i długości do 8 m. Suwnice pobierają odpowiedni walec z regału i montują na linii.
Granulat rozgrzewany jest do temperatury 210°C, a powstała w ten sposób masa nanoszona jest na obracający się gorący walec. Gdy całość wystygnie, walec wyjmowany jest z gotowego cylindra i wraca na swoje miejsce na regale.
Cylinder przekazywany jest na stanowisko CNC w pozycji pionowej. Czteroosiowa maszyna wycina w nim wszelkie potrzebne otwory; następny etap to spawanie. Dzięki technologii nawojowej można uzyskać zbiornik i wannę wychwytującą razem, co znacznie podnosi wytrzymałość konstrukcji (mowa tu o konstrukcji AmargTank MultiLayer DoubleWall®.
Technologia modułowa, czyli AmargTank MultiPower®
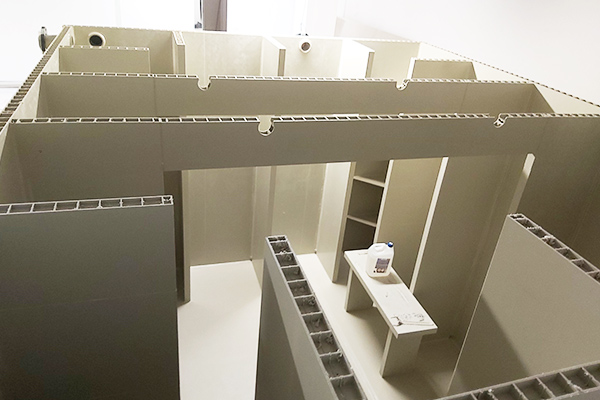
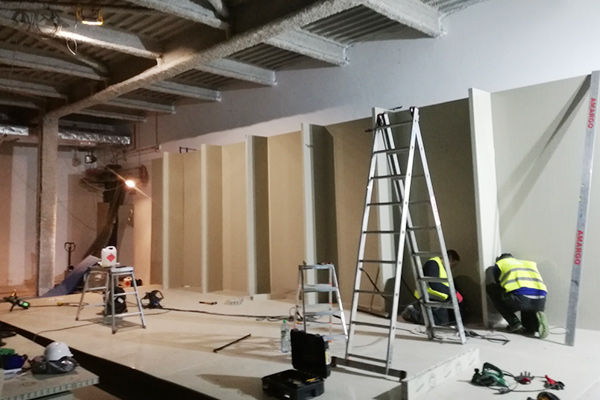
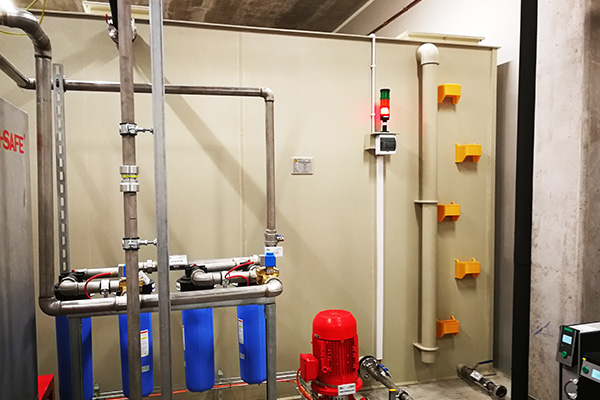
W materiale wideo nie poruszamy jeszcze jednej technologii tzw. AmargTank MultiPower®, która dotyczy zbiorników prostopadłościennych o konstrukcji modułowej i nieco mniejszych gabarytach. Warto jednak ją zestawić razem z pozostałymi. Ściany takiego zbiornika wykonywane są z prefabrykowanych płyt modułowych (żebrowanych, sandwichowych) MultiPower/Polystone CubX z odpornego tworzywa PP-COPO, HDPE lub PP-H o wymiarach 2600 × 1000 mm i grubości 50/57 mm. Dno i pokrywa (sufit) są wykonywane z płyty litej, np. z PP lub HDPE. Konstrukcja takiego zbiornika jest dodatkowo wzmacniana płytami tworzywa wspawanymi wewnątrz pod kątem 90o (wzmocnienia stalowe zbiorników mogłyby ulegać korozji).
Zbiorniki modułowe są wyposażane w króćce, przyłącza, rurociągi zasilania, zasuwy i zawory, systemy sterowania, pomiarów poziomu wody i komunikacji z centralnymi systemami sterowania zainstalowanymi w budynkach. Służą przede wszystkim do magazynowania wody rezerwowej (pitnej), przeciwpożarowej czy opadowej wewnątrz budynków.
Wycenimy Twój zbiornik i instalację
Wybierz odpowiedni formularz doboru i wyceny, uzupełnij dane i prześlij na adres eksperci@amargo.pl